November 19, 2015 Updated 11/19/2015
Email Print
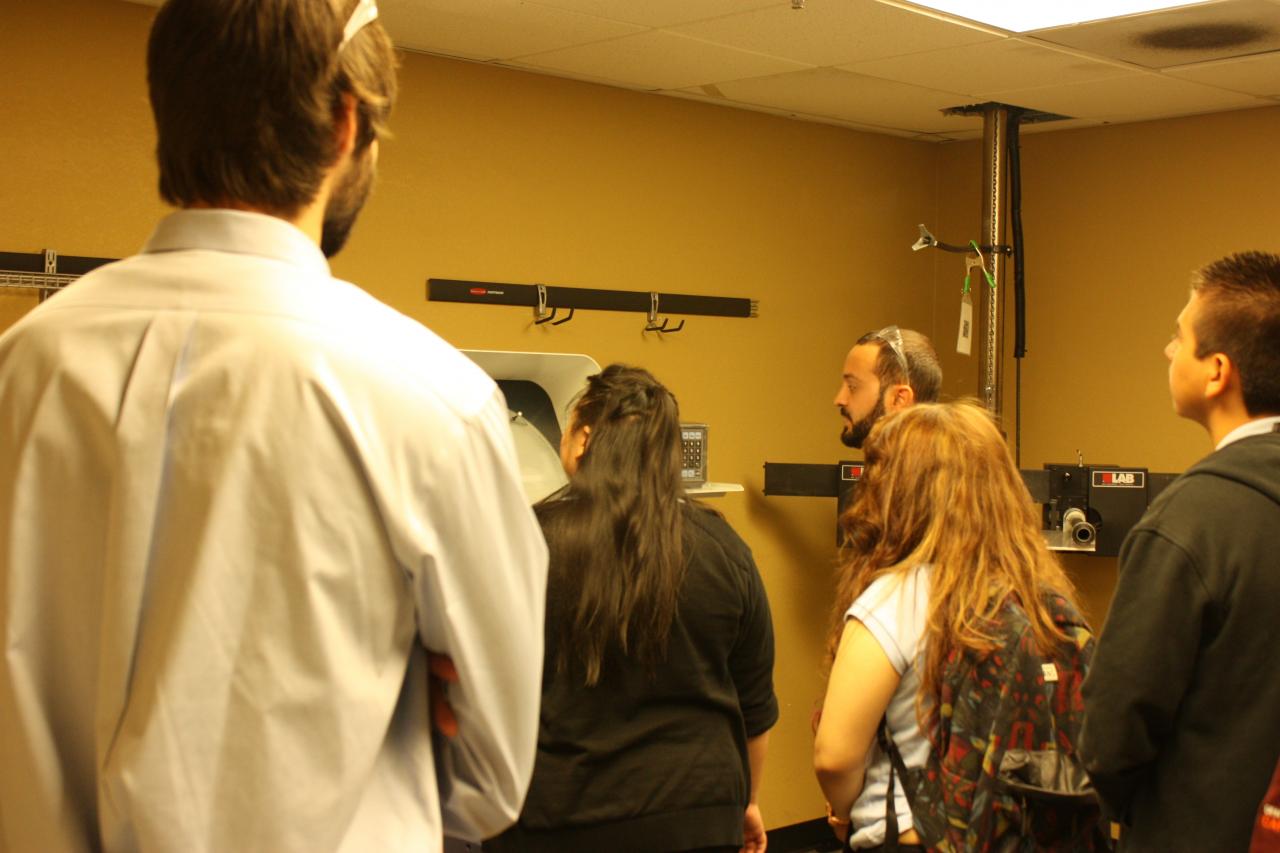
Intertech Plastics Inc. Students check out Intertech Plastics Inc. The company is leading a move to bring more apprenticeship training to Colorado.
Indianapolis — Colorado manufacturers are gearing up to do much more than advise and criticize the school systems they so desperately depend on for a skilled workforce.
They’re getting ready to turn their companies into extensions of the classroom in ways not really seen in the United States. Businesses are collaborating with schools to offer apprenticeship programs where 70 percent of high school students will spend three days a week in the workplace and just two days in the classroom.
And, injection molder Noel Ginsburg, CEO of Intertech Plastics Inc. in Denver, is leading the charge to try to improve outcomes for both students and business. It’s all based on what he has seen in Switzerland, which has topped the Global Innovation Index for the last two years.
“Students participate in a parallel learning system — the theory in the classroom and the practice in industry through paid, work-based training,” Ginsburg told a sold-out crowd at the 2015 Benchmarking and Best Practices Conference put on by the Manufacturers Association of Plastics Processors in Indianapolis Oct. 22-23.
“You might look at that and say that’s impossible,” he added. “It’s one of those ambitious goals that probably can’t happen but we’ll put it on paper anyway. I would have believed that until [this summer] when I spent 12 days in Switzerland.
Alpine model
Ginsburg was part of an entourage of educators, economic developers and trade association members that traveled to the European nation to see how businesses lead the effort to develop future talent through vocational education training (VET). Businesses start preparing students for highly skilled, high-demand jobs starting at age 15 or 16.
“The provider of education is primarily companies and industries, not schools, because we know what we need for our factories and businesses to run well,” Ginsburg said. “They leave it up to schools to teach reading, writing, arithmetic and core skills and they leave the rest up to industry. And it works.”
About 75 percent of Swiss students go for an apprenticeship certification while 25 percent pursue a four-year college degree. Most enterprises making up the Swiss economy — banking, financing, management, information technology, health care and manufacturing — offer VET.
“They realized that because they’re a small country if they were to be successful they had to have the best workforce,” Ginsburg said. “We can all buy the best equipment but it’s who drives that equipment that really makes the difference.”
The Swiss banking industry recently invested $ 20 million into its training system to make sure its talent pipeline is full, Ginsburg said. Regardless of the industry, apprentices earn about $ 800 a month, he added, as they spend most of the week in the field learning to do jobs that generally start at $ 55,000.
“Every year companies post the jobs they think they will need apprentices for the next two to four years,” Ginsburg said. “If there are no jobs being created, there are no apprenticeships being created. So you can’t study an apprenticeship where there isn’t going to be opportunities for you. It’s a very market-driven system and a very powerful system.”
While on a VET tour, Ginsburg said he asked a young apprentice why he chose the program.
“He said — almost all of them speak English — when I was in class and they were telling me about tolerances and dimensions, I didn’t care. But when I’m making this component for this machine, if it isn’t within one-hundredth of a thousandth, it won’t work. So they are connecting the theory with the practice,” Ginsburg said.
In a lot of cases, apprentices stay with the company where they earned while they learned. They start out making a middle-class wage and the employer ends up with a consistently productive workforce. It’s a proven solution for businesses to recruit, train and retain highly skilled workers, Ginsburg said.
“It’s highly profitable because can you imagine having someone come into your business who actually knew what they were doing before they graduated,” he asked plastics processors.
Because of the apprenticeship programs, the unemployment rate for Swiss youth ages 15-24 is 3.7 percent compared to 16.3 percent for Americans ages 16-19, according to the latest figures released respectively by the State Secretariat for Economic Affairs in Switzerland and the U.S. Bureau of Labor Statistics.
In the United States
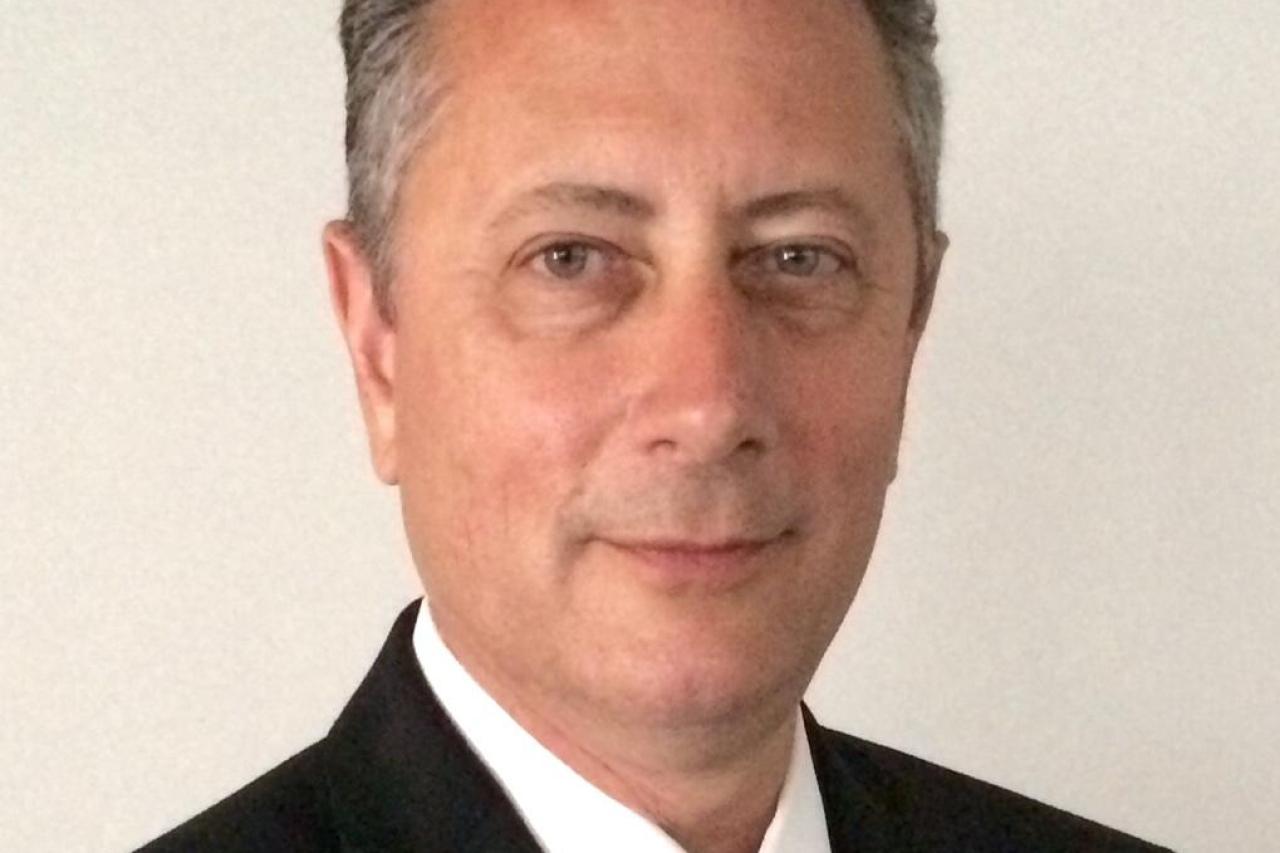
Ginsburg
About 28 percent of the U.S. population obtains a four-year degree or higher, according to Ginsburg.
“The remaining 70 percent? Good luck to you,” he said, explaining why he is pushing hard “to create a system that works for everyone” in Colorado.
An apprenticeship system would benefit taxpayers, too, according to Ginsburg.
“It doesn’t go to the public and say give us more of your tax dollars,” he said. “Let’s take the existing dollars and repurpose them in a way that provides the outcomes that we want.”
In May, Colorado passed several new laws with bipartisan support to revamp their education system. The legislation allows students to move from classroom work to training opportunities and then employment; expands a community college program to train workers at specific companies; and offers companies a $ 5,000 incentive for every new internship or apprenticeship created. At least half of the incentive must be paid to the intern or apprentice.
About 1,000 prospective apprentices are already getting “soft skills” training and an orientation to manufacturing ahead of the pilot career program that starts in 2016, Ginsburg said.
In the meantime, Colorado is developing a new curriculum along with certified centers of learning for the future apprentices Ginsburg expects a 10-year rollout across the state with the Colorado Advanced Manufacturing Alliance on board early to do the testing and certification for that industry.
“The school system has the benefit of graduating more students and that’s what they’re in business to do,” Ginsburg said. “For us, as employers, productivity outweighs the training costs resulting in a profitable model. We hope in the long term it will eliminate the critical skills gap.”
The skills gap can be costly for businesses. Intertech, which makes totes, laundry baskets, baby products and medical devices, lost an estimated $ 1 million in sales in 2013 because there weren’t enough qualified workers for the 50-press plant, according to the Denver Business Journal.
Smart business
In the U.S., manufacturing is the No. 2 contributor to the gross domestic product (GDP) — behind health care — and at 16-17 percent it is almost back to where it was in its hey day, Chris Kuehl, chief economist for the Fabricators and Manufacturers Association, International, told MAPP conference-goers.
Kuehl put the massive size of the U.S. GDP into perspective with a few comparisons. It’s twice the size of the nearest competitor, which is China, and many states have GDPs that are comparable to other countries.
“[New Jersey Gov.] Chris Christie and [Russian President] Vladimir Putin control the same size economy,” Kuehl said. “The GDP of New Jersey is the same as Russia. The GDP of Canada is the same as Texas. Argentina is the same size as Dallas.”
And, where does manufacturing fit in?
“All by itself, manufacturing in the U.S. is the 10th-largest country in the world. Just our manufacturing GDP is bigger than the entire GDP of India,” Kuehl said.
Automation allowed the industry to increase productivity while decreasing its workforce, however, there are still many positions going unfilled.
“It is kind of ironic that we’ve seen a tremendous decline in the number of people working in the field and we have a job shortage at the same time,” Kuehl said. “We can’t find people to work in manufacturing.”
Ginsburg is trying to address that in Colorado and urging others to get on board. He said his staff will share all apprenticeship information with anyone who wants to build out similar programs in other states. Business leaders have to do more than sit on school advisory boards on a limited basis and complain when skill needs aren’t met, he said.
And, donations for college scholarships and foundations only go so far. Ginsburg should know. He’s a founding member of the Colorado I have a Dream Foundation, which encourages students at risk of dropping out of school to graduate and then rewards them with $ 4,000 post-secondary scholarships. He and his wife, Leslie, are sponsoring a class of 42 students right now.
Intertech has internship and mentoring programs, too, but Ginsburg said he struggled with how to offer “a better path” for entire cities and states until he visited Switzerland.
“An investment in education is no longer philanthropy but rather a business strategy,” Ginsburg told conference attendees.
And, ignoring such a strategy means businesses may have to outsource jobs to fill them with skilled workers and the U.S. will risk its position as an international leader.
“I think this is imperative for our country and our businesses,” Ginsburg said. ”At the end of the day, if you and I as business leaders and owners don’t think differently, this won’t happen. And, we’ll find ourselves continuing to erode our competitiveness. But if we choose to engage, we can truly change, I believe, the world.”