January 15, 2016 Updated 1/15/2016
Email Print
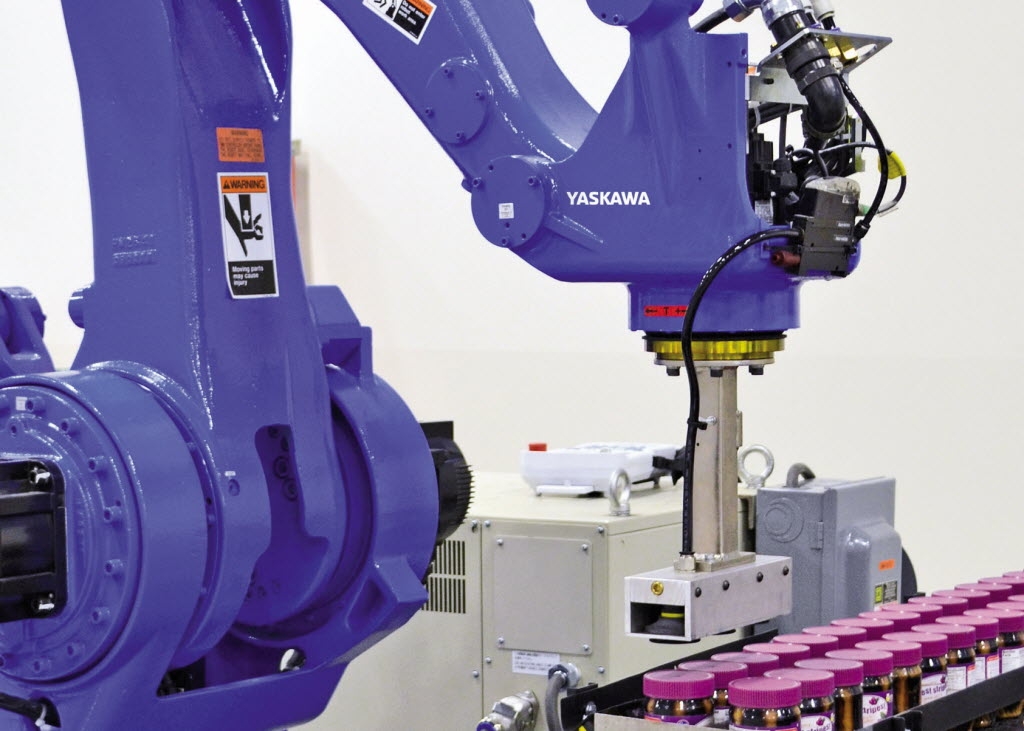
Yasakawa Motoman The pictured robot system employs a vacuum-cup-equipped arm like Berry Plastics Corp.’s new robot used for packing multiple bottles into re-shipper boxes.
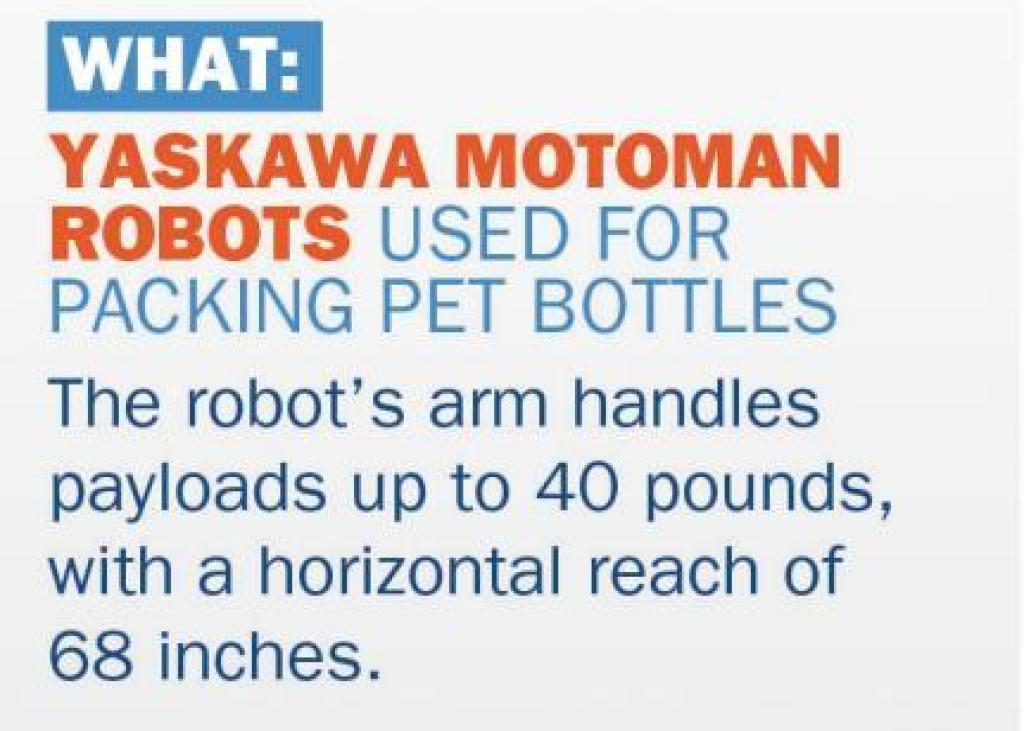
In the plastics industry, processors know Yaskawa Motoman for its articulating-arm robots. But the company also makes robots for packing parts — and a system installed for Berry Plastics Corp. is the first one of Plastics News’ Best Practices articles.
Once a month, we will bring you innovative work on machinery, technology, people and business organization.
To kick off Best Practices, and the New Year of 2016, we look to Berry’s factory in Dunkirk, N.Y. Before the robotic system, two full-time employees worked an eight-hour shift to pack PET bottles, made in a blow molding machine. Now they have moved into other work in the factory, officials said.
Yaskawa Motoman, based in Miamisburg, Ohio, designed the portable case-packing automation. The robotics company teamed with its systems integrator partner developed solution: The blow molding machine sends PET bottles along a tabletop conveyor to the packing cell, which includes a six-axis Yaskawa HP20D robot and the company’s MLX200 controller.
The robot’s arm handles payloads up to 40 pounds, with a horizontal reach of 68 inches.
Berry installed the portable case-packing automation cell in November 2014.
Engineers integrated the robot arm and controller and built the cell so factory workers could move the system between two production lines. The vacuum-cup-equipped robot arm picks multiple bottles into re-shipper boxes. The cell integrates with a tape machine to automatically form the boxes.
Yaskawa Motoman officials said the MLX200 controller lets plant engineers program and control the robot through the factory’s programmable logic controller, using Ethernet via one table tied to a hub. Employees can handle all robot programming within the Allen-Bradley RSLogix 5000.
Rick Flynn, senior controls engineer at the systems integrator, said the new method of communication gives “seamless integration to the PLC control systems,” allowing the PLC programmer to control everything robot-related inside the PLC’s ladder logic.
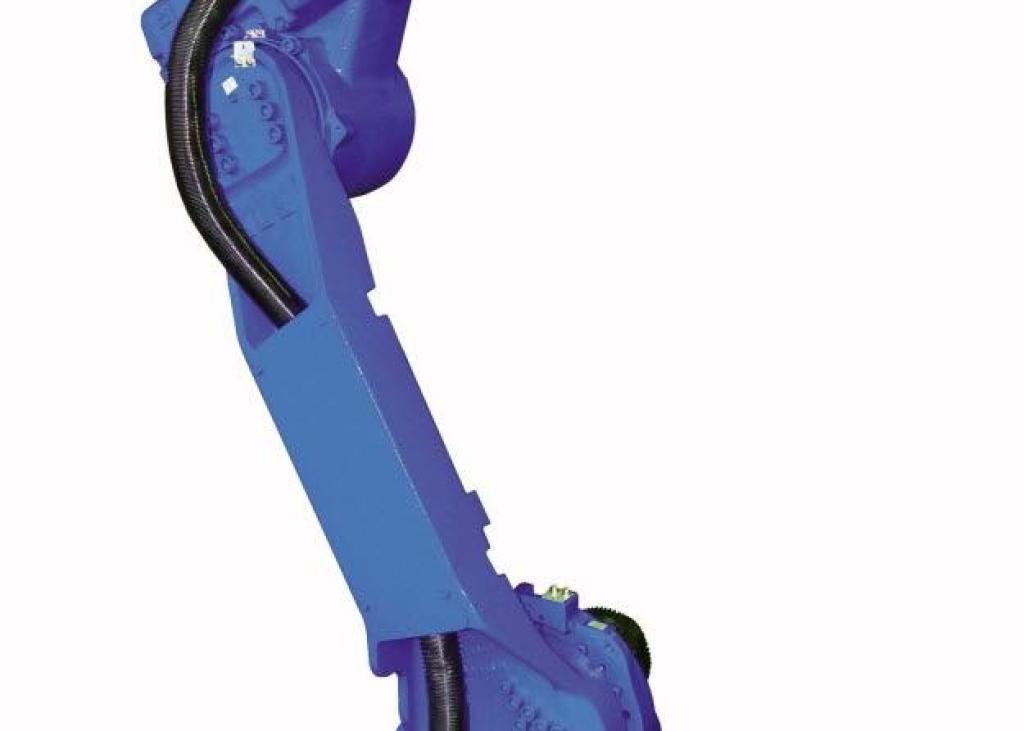
Darren Spinler, process engineer for Berry Plastics, said the controller is simple to use. “For other applications, we have to call in the OEM and write a program if we want to make a change. The MLX2000 calls out where the robot will go, and we just teach the robot the touch points. For example, one point might be a bottle pick. We use the control and ‘job’ the robot, which records the position of all six axes. Once learned, it can always go back to this point.”
And now, Berry’s Dunkirk plant can operate its line around the clock, instead of being limited by eight-hour shifts.
This case-packer robot hits all the touch-points of automation today: Easy to use, quickly adaptable for new jobs, and replacing a tedious job done by humans.
“If we’re converting the line for a new product, we change the robot’s picker arms, which takes about four minutes,” Spinler said. “There are a couple of airlines to connect and six thumbwheel knobs to turn for putting new tooling in place. We then hit the load recipe on the controller and adjust the conveyor and rails. From start to finish, the changeover takes 30 minutes.”