January 15, 2016 Updated 1/15/2016
Email Print
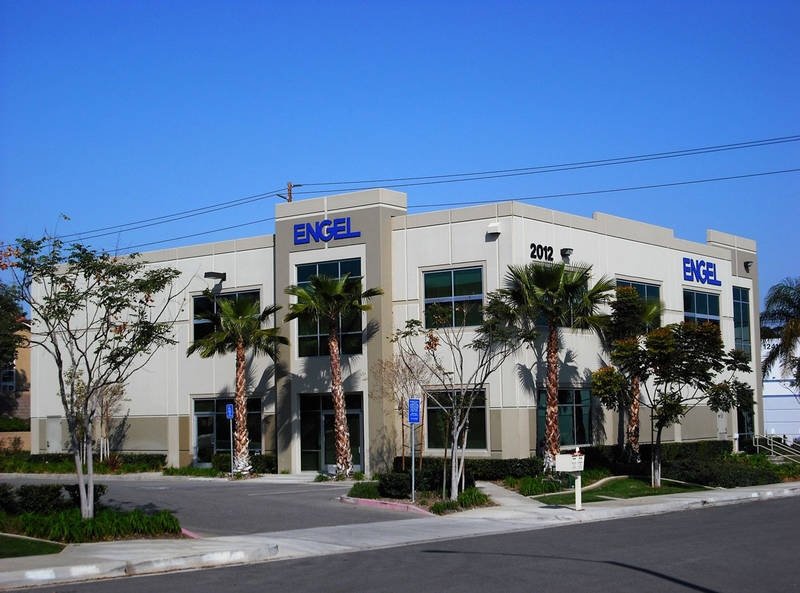
Engel North America Engel North America’s Corona, Calif., technical center.
Corona, Calif. — Innovations in liquid silicone, cube molds, in-mold decoration and Industry 4.0 were featured in a technical symposium at Engel North America’s Corona technical center.
Markus Lettau, West region sales manager for Engel North America, presided at the Jan. 13 symposium.
In liquid silicone, Bluestar Silicones USA Corp. has developed fast-curing self-bonding self-lubricating LSR Select in a conceptual change from traditional systems for two-part liquid silicone rubber injection molding.
“LSR Select shifts control to an inline process from chemistry,” and is “adjustable to optimize the curing process,” said Umar Latif, Bluestar Silicones technical services manager for North American elastomerics markets.
Bluestar and Graco Inc. of Minneapolis partnered in the custom design of novel equipment with servo pumps for close control over LSR Select formulation and processing.
Kipe Molds Inc. of Placentia, Calif., made tools, and Roembke Manufacturing & Design Inc. of Ossian, Ind., conducted trials with one-cavity prototype molds for a matt seal connector, duck bill valve, solution seal and baby bottle nipple. Latif said cure time reductions ranged from 20 percent to 50 percent.
The development in the York, S.C., technical center is applicable to other global locations of Bluestar Group. The center opened in 2012 and utilizes two Engel injection molding machines.
Next-generation Flexi-Cube
Brush manufacturing equipment maker Boucherie Borghi Group of Izegem, Belgium, is nearing introduction of a new generation of its Flexi-Cube technology.
The development will “further enhance our design and provide more flexibility,” said Sherman McGinnis, injection mold sales manager for Boucherie USA Inc. in Knoxville, Tenn.
The current Flexi-Cube contrasts with traditional cube molds. Parts move about the Flexi-Cube’s center section, have flexible travel distances and achieve transfer times as low of 0.7 of a second per station. In a standard cube mold, the entire center section rotates with movements restricted to 90 degrees or 180 degrees.
In-mold decoration
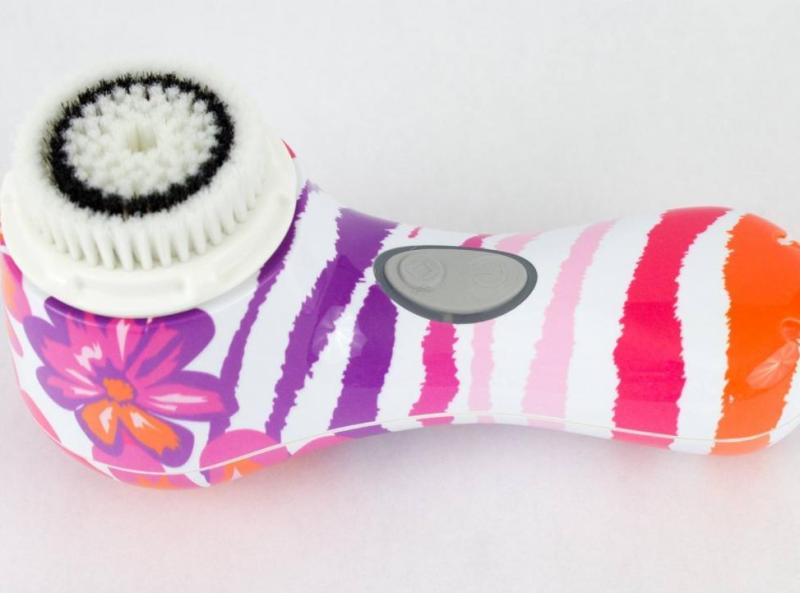
In Mold Decorating Association ZoMazz Inc. worked with Phillips-Medisize Corp. on the in-mold decoration for the Clarisonic Mia 2.
Jonathan Drake, CEO of ZoMazz Inc. of Monterey, Calif., described the firm’s patented technology for scalable digitized in-mold decoration as a technique many “processors don’t have.”
The young firm can qualify a plastics processor on the precision technology or provide finished product through contract molders. “We can do one or millions,” he said.
ZoMazz received the gold award for the best injection molded durable part in the 2015 competition of the Skokie, Ill.-based In-Mold Decorating Association. The label is used on the Clarisonic Mia 2 facial cleansing brush. Phillips-Medisize Corp. molds the product.
Engel’s ‘Inject 4.0’
Engel’s Wolfgang Degwerth described the company’s technology concept Inject 4.0 as its vision to extend the idea of Industry 4.0 relating to cyber physical systems. Degwerth is vice president of sales and customer service for Engel Machinery Inc. in York, Pa.
While Industry 4.0 aims “to handle the increasing complexity better,” Engel’s Inject 4.0 looks toward future applications involving preventive maintenance, predictive maintenance and cloud services for early adopters and smart factory advocates, Degwerth said.
Engel plans to introduce a solution for condition monitoring at K 2016, set for Oct. 19-26 in Düsseldorf, Germany.
Engel’s Joachim Kragl described machine embedded intelligence including iQ software. Kragl is director of advanced molding systems and processing for Engel Machinery.
The iQ software is now standard for weight monitoring on Engel electrics and optional for weight control. An iQ clamp control can reduce wear and automatically find the clamping force.
Kragl talked about Engel’s intelligent mold control including the e-flomo version for closed loop control and e-flomo premium for fully remote control. Engel showed both versions at the 2015 Fakuma show.
Lettau discussed Engel’s Fast Lane program that can provide quick delivery “ready for any demanding application” as needed to meet customer requirements.
Lettau underscored the value of Schwertberg, Austria-based family-owned Engel Holding GmbH as a “stable long-term partner” able to “increase competitiveness for customers.” The Americas account for 22 percent of Engel sales, Europe for 58 percent, Asia for 17 percent and elsewhere for 3 percent. In addition to Corona, Engel locations in the Americas are in York, Pa., as Engel Machinery; Waterloo, Ontario; El Marques, Queretaro, Mexico; and Cotia, São Paulo, Brazil.
During the day, Engel machines produced bursting discs for 1-milliliter safety syringes on a smart manufacturing cell, ran a four-cavity duck bill mold with in-mold slitting using Bluestar liquid silicone and demonstrated use of ZoMazz digital in-mold decorating with a single cavity mold.