January 29, 2016 Updated 1/29/2016
Email Print
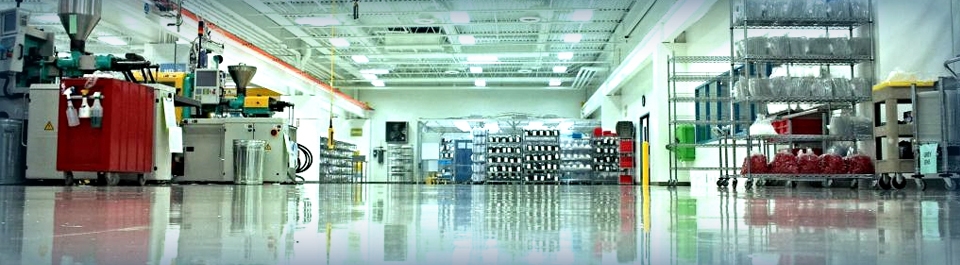
Medical molder Medbio Inc. is ramping up production of its 22nd injection press to meet growth and provide backup molding capacity.
“We are growing very steadily,” said John Woodhouse, director of sales and marketing, in a phone interview. “We have several new programs.”
Medbio purchased a new Arburg 470C 165-ton hydraulic press with a five-ounce shot size. The machine is equipped with advanced control systems, in tune with the firm’s emphasis on controlling the molding process.
“Like most of our Arburg machines, this press has cavity-pressure sensing capabilities, using Kistler-brand sensors,” Woodhouse explained. “This machine is also equipped with a hydraulic core pull and pneumatic valve gate control, and will have an automated packaging cell.”
Medbio’s presses, all Arburgs, are hydraulic or hydraulic/hybrid machines, which it claims can be cleaner than all-electric presses with a lubricated ball and screw. The firm stresses screw design and shot size are critical for precise molding. Woodhouse said tight tolerances are demanded for medical parts, and the firm’s usage of a broad spectrum of resins also means it has to closely control the molding process.
Medbio’s work includes micro molding of parts typically weighing less than a gram. For such jobs it can attach an Arburg micro molding module to one of its presses. The company’s press clamp range runs from 17 to 220 tons. It does insert and over-molding with a fixed vertical rotary press. It molds dozens of resin types, from commodity materials to engineered polymers.
The privately held company employs more than 125 on three shifts in its 45,000-square-foot facility in Grand Rapids, Mich.
Woodhouse said integration of its own tool-building shop into its molding programs has been going well and allows Medbio to offer short lead times and flexibility to add new programs. About two years ago it bought Concept Molds Inc. of Schoolcraft, Mich., to do make much of Medbio’s tooling in house.