April 1, 2016 Updated 4/1/2016
Email Print
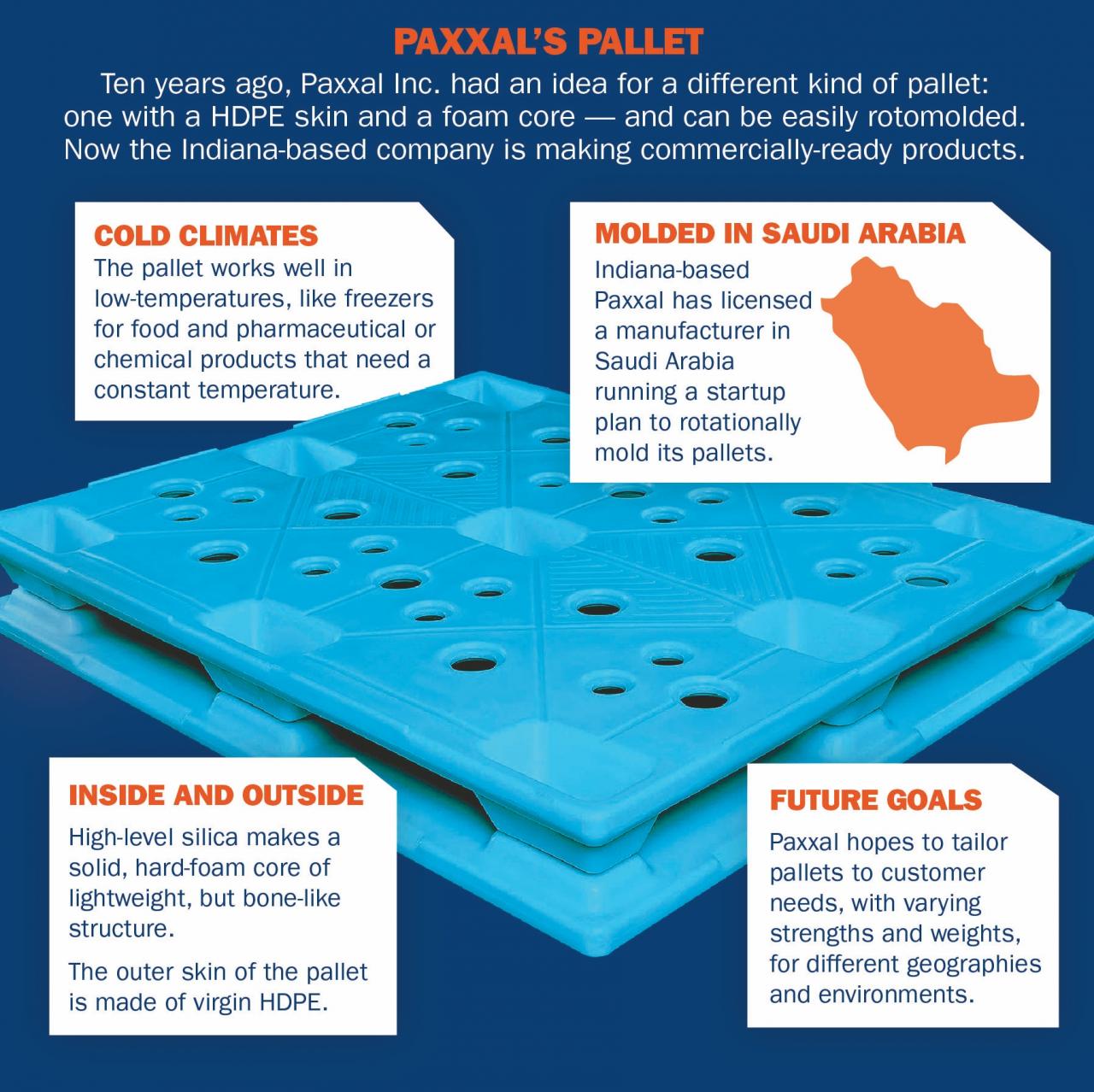
After a 10-year materials development period, Indiana-based Paxxal Inc. has licensed a manufacturer in Saudi Arabia running a startup plant to rotationally mold its pallets — using high density polyethylene and silica.
Paxxal developed the process, which uses automated rotomolding equipment and Paxxal’s expertise in blending the materials, using a proprietary “unifier.” Michael Laible, sales director for the Eastern United States, called the unifier “our secret sauce.
“We’re not just another plastic pallet company. We’re bringing a new material to the market,” Laible said. The Saudi Arabia plant began making commercially ready products late March.
MaryPat Freeman, Paxxal’s sales director for the Midwestern United States, said the company’s rotomolded pallet has a solid core of a lightweight, but bone-like structure. It works well in low-temperature environments such as freezers for food and pharmaceutical products, or chemicals that must be kept at a constant temperature, she said.
“One of the biggest hurdles of plastic pallets is when you put them in a freezer.” Freeman said, adding that the surface can get glossy and slippery. “Because our pallet is filled, it behaves differently in that environment.”
Three Paxxal officials talked about their company on March 25: Ezzeldin Elmassry, global director of treasury and investment; Freeman; and Laible.
Paxxal employs nine people at its Noblesville, Ind., headquarters. The under-license production facility in Saudi Arabia employs about 40, Elmassry said.
Paxxal is not disclosing details about the rotomolding machine or the process for this story. Instead, the three company executives want to talk about their product. Elmassry said Paxxal is using HDPE made by Saudi Basic Industries Corp., which is “the kind of grade that we’re looking for.” The outer skin is virgin HDPE. And the high-level silica produces a hard-foam core.
Paxxal is exhibiting at the Modex trade show for the first time, as it runs April 4-7 at Atlanta’s Georgia World Congress Center. Paxxal will be at Booth 1255 during the trade show dedicated to supply chain equipment and technology.
Elmassry explained Paxxal’s background. The concept began about a decade ago, as materials experts looked at creating something with an HDPE skin, as well as a foam core made out of readily accessible material — and can be easily rotomolded, he said.
Paxxal in Noblesville is the material-engineering test facility, the location of the expertise.
Elmassry said the developers looked for a mass-produced product that could use the material’s benefits.
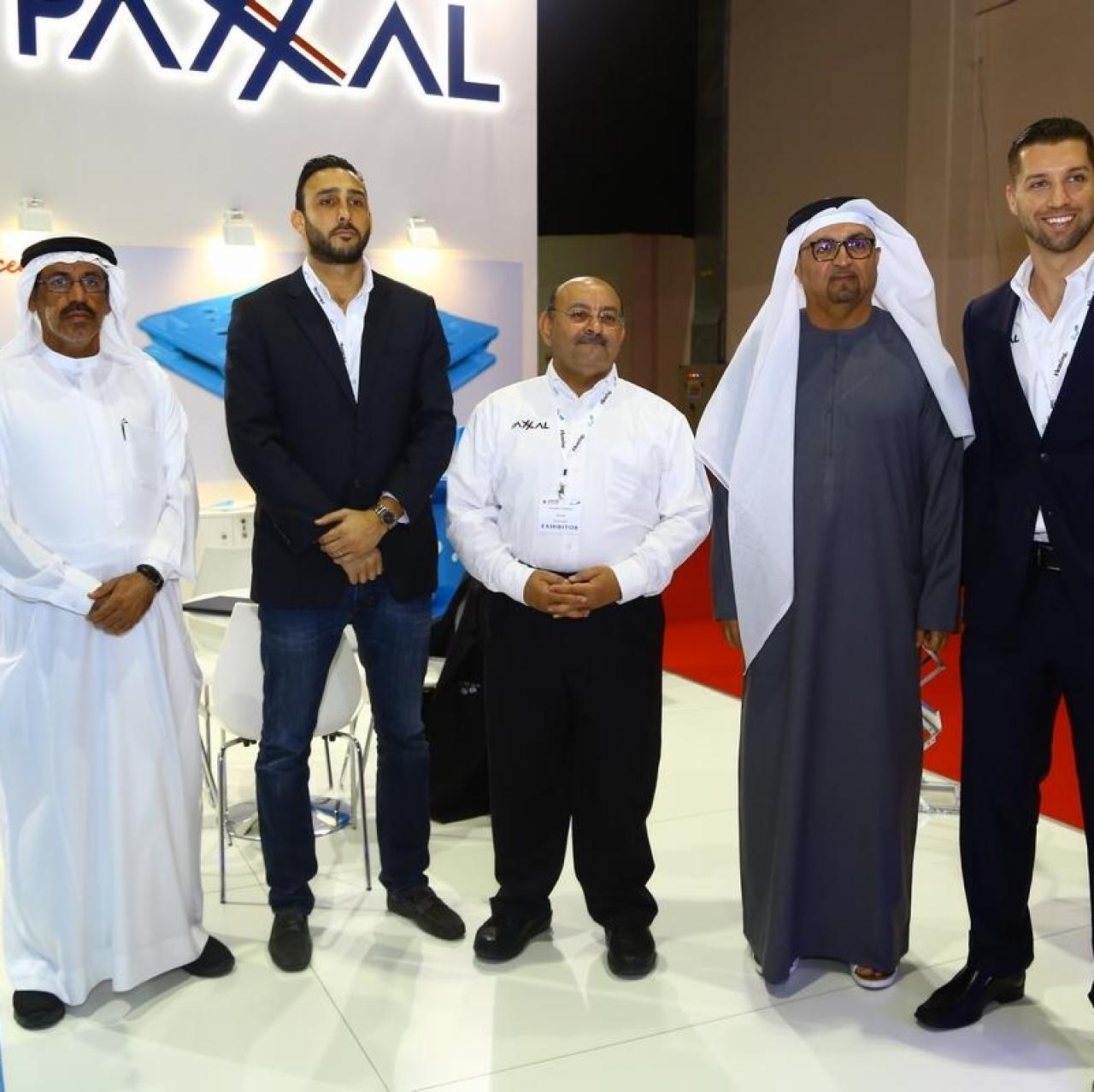
Paxxal Inc. Ezzeldin Elmassry, global director of treasury and investment for Paxxal, center, and Michael Laible, sales director for the Eastern United States, far right.
“The pallet emerged as the most used. There were billions of them used around the world,” he said. There is a significant movement from wood to plastic pallets. “We thought at the time it was a very promising space to get into.”
The challenge with traditional rotomolding is the process is relatively slow and labor-intensive.
So Paxxal looked at a redesigned rotational molding process and material feeding system, and features like cooling and a high level of automation, to achieve efficient production at high volumes, Elmassry said. The Saudi Arabia plant is state-of-the art, he said.
Freeman said the high-volume pallet manufacturing will help make the Paxxal pallets economical in price — to go with their durability.
For the last year and a half, Paxxal tested the pallets with some customers to get feedback, Freeman said.
The material, the process and the design are patented, the company leaders said. And Laible notes that the plastic-and-silica combination mean the pallets have no black market value — no reason for thieves to steal them. “The only value is to us,” he said,
Elmassry said in the future, the company will make pallets with different formulations and combinations of materials — for example, to tailor pallets to customers in a variety of geographies, environments, and designing pallets in varying strengths and weights.