April 22, 2016 Updated 4/22/2016
Email Print
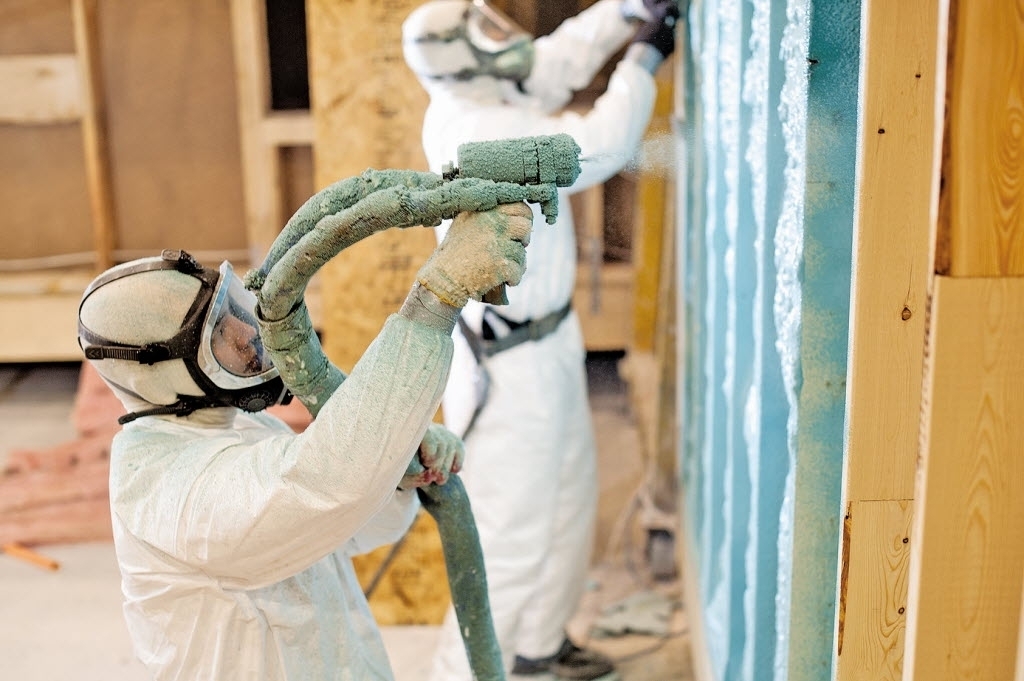
Spray Polyurethane Foam Alliance Spray foam insulation offers a variety of benefits for homeowners looking to create new living spaces from attics, and improve roofs.
Spray polyurethane foam (SPF) sales topped $ 1 billion in 2015 by most estimates after another solid year of growth due to increased activity in construction and home improvement projects.
Manufacturers reported some 460 million to 490 million pounds of SPF, which is used for roofing and insulating, were sold last year in the U.S. and Canada, according to Rick Duncan, technical director of the Spray Polyurethane Foam Alliance (SPFA) of Fairfax, Va. At a cost of roughly $ 2.25 a pound, SPF reached the milestone of being a $ 1 billion market in 2015.
“It’s difficult to give precise numbers but we’ve been seeing continued strong growth over the last decade,” Duncan said in a telephone interview, noting that the American Chemistry Council helps track sales by pounds of SPF chemicals sold and not dollars.
Duncan said he is still waiting for final numbers but it looks like residential insulation applications drove sales growth again.
“I have year-over-year data from 2013 to 2014 and we’re seeing growth on the residential side on average of about 15 percent. If you go back to 2013 over 2012 it’s about the same, about 16 percent,” Duncan said. “When you look at the housing market and the construction market, it’s not growing at that rate so we’re getting a lot of retrofit and we’re gaining market share.”
SPF competes mostly against fiberglass and cellulose for residential uses, and against foam boards on the commercial side in the U.S. insulation market, which is projected to grow 6.6 percent a year through 2019 to $ 10.3 billion, according to Freedonia Group Inc., a Cleveland-based industry market research firm.
“Fiberglass and foamed plastic are by far the most prevalent types of insulation, together accounting for 93 percent of the market by value,” Freedonia analyst Nick Cunningham said in a news release.
Fiberglass will remain the market leader by weight, he added, pointing to a forecast that shows demand reaching 4.5 billion pounds valued at $ 4.9 billion in 2019. Demand for foamed plastic insulation is projected to grow to 2.4 billion pounds valued at $ 4.7 billion in 2019.
Unvented attics popular
The use of SPF in residential attics is one application that’s on the rise. Homes have been built with ventilated attics — usually screened vent holes under the eaves — for centuries to allow warm air and moisture to escape and to keep the roof cold in the winter, which stops the formation of ice dams.
However, the acceptance of unvented, conditioned attics has been increasing since 2006, when the International Residential Code started permitting them, partly in response to builders wanting to locate HVAC equipment up there. SPF is one of the building products used to turn attics into conditioned spaces so HVAC systems can operate efficiently and homeowners can pick up storage area that’s about the same temperature as the rest of the house.
SPF comes in open- or closed-cell foams and either can be used for unvented attics. Closed-cell SPF, which is more rigid and stronger, often is recommended for the pitched part of the roof.
“Insulation is put right under the roof deck in the pitched part of the roof and spray foam is best for that because it adheres and stays in place,” Duncan said. “There are tens of thousands of homes now insulated that way and it can save about 10 to 15 percent on your heating and cooling costs. That’s pretty substantial. And for places like Florida, California and Texas, where you have no basements, it adds a conditioned storage space to the house and people really like that. You can put stuff up there without worrying about candles melting or things getting ruined by the heat.
“Unvented attics have really helped our industry when we talk about that 15 percent growth. We’re seeing that a lot of homeowners are using unvented attics as a retrofit.”
Sales of SPF for home improvement projects are strong enough to outweigh uncertainties about new home construction, Duncan added.
“We’re seeing some information that the housing market is getting better and then we see other reports that it is not,” he said. “We’re not too concerned because we’re seeing a lot of growth from retrofit. People are staying in existing homes and saying let me make my house more efficient. How can I do that? And SPF in the attic is the easy way.”
Roof benefits, too

Spray Polyurethane Foam Alliance SPF insulation sales are now topping $ 1 billion in value.
SPF actually started as a low-slope roofing material for commercial buildings in the 1960s, but sales didn’t take off for another 30 years when it became popular as an insulation product. These days, about 10 percent of sales are for roof applications.
“Spray foam puts the insulation and water seal down in one operation and then you cover it with a coating to protect it from the sun and you’re done,” Duncan said. “It’s a lot less labor intensive, and in some cases less expensive, than most roof systems. But it really hasn’t grown that much.”
New certification programs and training for contractors have provided more variety in the way roofs are assembled, but weather limitations remain.
“You can only spray foam in dry weather and it has to be warm,” Duncan said. “There are very few spray foam roofing contractors in Seattle because it rains so much and they don’t have a lot of time to spray. But it’s very popular in Arizona and Texas, where it’s dry and they can work all year.”
Closed-cell SPFs also are finding their way into roofing systems in hurricane-prone areas, where they are applied underneath plywood roof decks to increase the wind-uplift resistance up to three times.
“That means if you take an older home in Florida, let’s say built before 2000, and if you spray just 2 inches of closed-cell foam underneath that plywood, it will not lift off in a Category 3 hurricane whereas it would in the past,” Duncan said. “And, the closed-cell foam provides a water barrier. Most houses will lose their shingles and underlayment in a hurricane, and that causes the roofs to leak. When water gets inside the houses your drywall fails and the interior of the house can be totaled even if the roof is in place without shingles. With the closed-cell foam it seals off the plywood and the home will survive. You’ve got to put new shingles on but the inside of the house stays dry.”
Although SPF competes against foam board as an insulation product, upstream chemical manufacturers that supply both markets are urging manufacturers to work together when it comes to wall systems.
Dow Chemical Co.’s Building Solutions and BASF SE both are promoting high-performing wall systems made with foam board as the sheathing instead of oriented strand board and about 3 inches of closed-cell SPF in the wall cavity to seal air leaks and add strength. SPF replaces fiberglass insulation in this construction method.
“We think those two products together make the best residential frame wall that you will find,” Duncan said.
Certifying contractors
A lot of contractors got into the SPF business during the construction slowdown, despite the high start-up costs. Spray foam rigs sell for $ 50,000 to $ 100,000, and although the process looks as easy as spraying paint, Duncan said it isn’t.
“We had carpenters and electricians say, ‘I’m not doing any work but I hear spray foam is growing — let’s get into that,’” he said. “But unless they were properly trained they often failed.”
To keep the profession from getting a black eye from SPF jobs gone awry and to address concerns of the Occupational Safety Health Administration (OSHA), the alliance created a professional certification program in 2013. More than 1,000 people have since been certified to various levels.
“We’re trying to raise the bar,” Duncan said. “Some manufacturers will certify their customers but when they do bad work, they don’t always uncertify them. We said that’s not sufficient so we created a program that follows the international standard and is based on industry consensus. And, we do revoke certification if someone isn’t doing something safely.”
For example, one certification was revoked for six months when a contractor posted a YouTube video of himself applying spray foam without personal protective equipment, such as face masks, Duncan said.
To obtain SPFA certification, each installer must be trained by the factory for two to three days. A business can’t send just one person for training and then have them train their co-workers when they get back.
Other challenges
SPFA also is helping contractors meet new OSHA requirements for working in confined spaces like manholes, tanks, crawl spaces and attics. New regulations aimed at preventing worker deaths and injuries — there are about 8 fatalities and 800 injuries annually — went into effect recently following a temporary stay of enforcement but the National Association of Home Builders says it “continues to negotiate with the agency to clarify the rule’s application to residential home building.”
In general, the rule requires employers to evaluate job sites, control physical hazards, monitor atmospheric hazards, and train workers and supervisors to handle emergencies.
“So many people are working in attics now and not doing it safely,” Duncan said. “Not just the spray foam people but those working on HVAC systems, the cable guys installing wires, and others. If you don’t step in the right place, you’ll put your foot through the ceiling, which is a hazard. There are also trip hazards or you could bump your head on the rafters. It can get too hot or if there’s a fire, how do you escape.”
Training contractors to avoid these problems is important, Duncan said, otherwise government regulators will start requiring them to obtain permits to work in attics.
“That would mean a lot of administrative details that would really escalate the cost of doing any work in the attic,” he said. “You have to have someone stand outside the door and monitor who goes in and out. You have to have a rescue team on duty. We’re telling our people if you don’t want to do those things then there are general safety requirements to follow in advance. It’s an education process.”
The alliance also is dealing with concerns about flame retardants used in foam.
“The one we use has been evaluated by the European Union, which says it is not a problem,” Duncan said. “But chemically it’s similar to flame retardants that are a problem so we’ve been grouped together and the [U.S. Environmental Protection Agency] is looking at what we’re using.”
The alliance also is working with EPA and the Consumer Product Safety Commission to develop methods to measure emissions from foam that could affect the air quality inside buildings.
“Those groups are asking us to characterize and measure certain emissions that come from spray foam when it is used as a building product,” Duncan said. “The industry is developing special tests just for the chemicals used in spray foam. We’ve been working on that for 3 to 4 years. It’s still ongoing but we’re getting close to the end.”
The SPF industry also is tackling concerns from architects and specifiers about its petroleum-based products, which come in 55-gallon drums, and whether they are bad for the environment.
“We do use petroleum but we did a life cycle assessment of our product over the 60-year life of a building where it was used to insulate air seals and you save about 250 times the energy used to make the spray foam,” Duncan said. The payback is huge. Not a lot of products can say that if you look at, for example, the petroleum used to make carpeting or other building products where there’s no payback. We have a positive payback.”