May 27, 2016 Updated 5/27/2016
Email Print
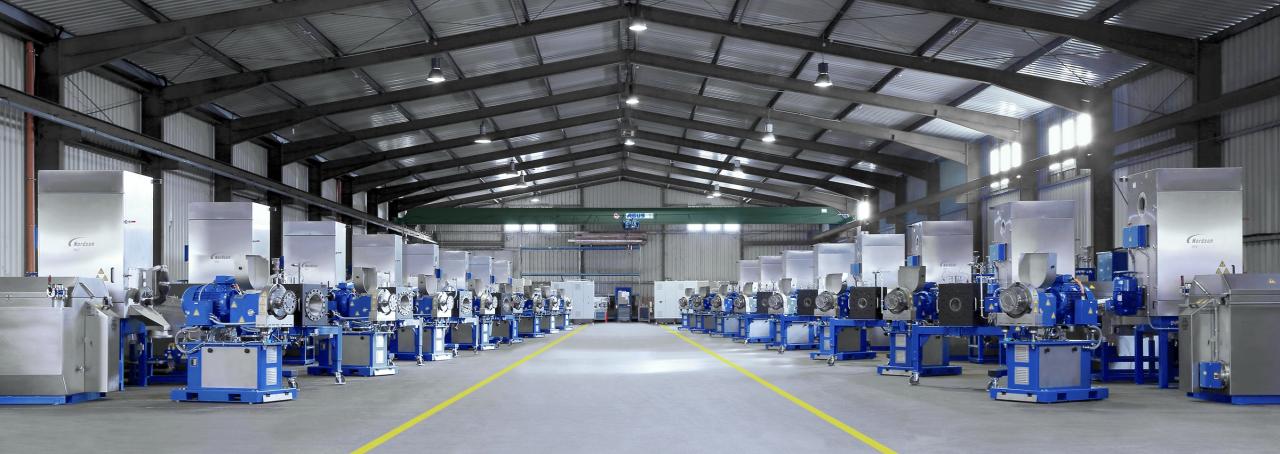
Nordson Corp. Nordson’s BKG brand CrystallCut PET pelletizing system, is being installed at the “largest PET plant in the world,” at Jiangyin Chengold Packaging Materials Co. Ltd. in China.
Shanghai — Nordson Corp. is targeting a growing market of plastics machinery makers in China seeking top-shelf components.
The strategy is based on a fundamental change in the Chinese plastics industry, as more and more manufacturers seek out precision parts, said John Keane, vice president for polymer processing for Westlake, Ohio-based Nordson.
“Every year, their machines get better. And they’re servicing a higher expectation from their customer. So they’re looking for a higher-quality component that has to hold up,” said Keane, speaking at Nordson’s booth at last month’s Chinaplas in Shanghai.
“We sell widgets,” quipped Keane. “We don’t sell lines. We try to be the key thing on a line, the technology that differentiates that line.”
Among the company’s many multinational customers is Ningbo-based Haitian International Holdings Ltd.
“Increasingly, the higher end of the Chinese market is seeking us out,” Keane said. “They’re looking for a support network if they export. Particularly the OEMs, they can ship anywhere in the world and we’re there to support them.”
Nordson serves the injection, extrusion and recycling-machinery sectors with dies, screws, barrels, filtration systems, pumps and valves — the fruits of a five-year acquisition binge that saw the longtime adhesives giant stockpile such well-established brands as Chippewa Falls, Wis.-based flat-die maker Extrusion Die Industries LLC (EDI), New Castle, Pa.-based screw-and-barrel maker Xaloy Inc., and two German companies that were subsidiaries of Kreyenborg Group: Kreyenborg GmbH, a maker of melt filters and screen changers, and pelletizer manufacturer BKG Bruckmann & Kreyenborg Granuliertechnik GmbH.
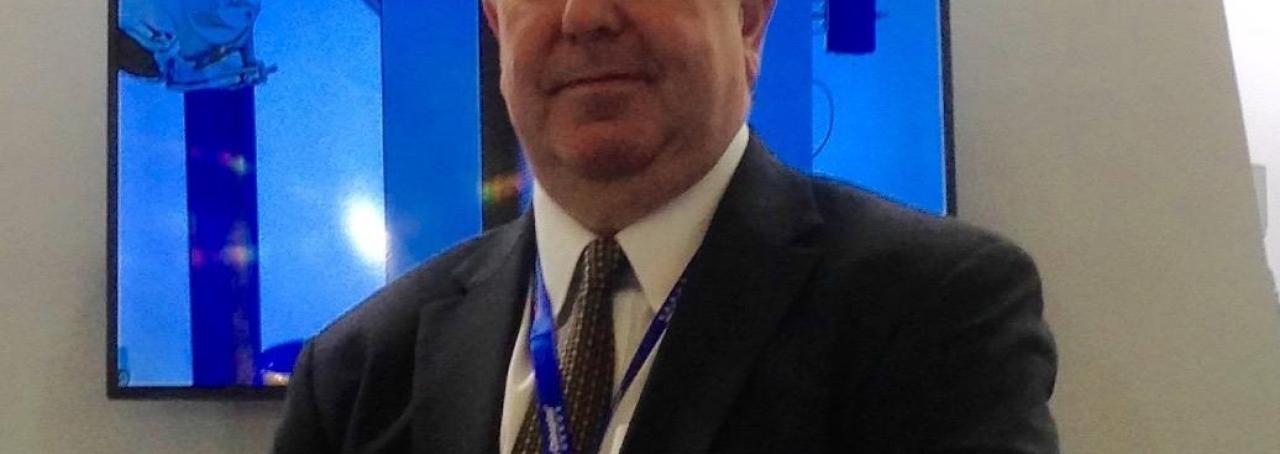
Kent Miller Keane
“The components business globally has been largely regional players. Nordson came with the idea of let’s take the best regional players, put them into a group and create a global components business,” Keane said. “The uniqueness of our model is that there are very few companies that line up head-to-head with us and can offer the same product anywhere like we can,” Keane said.
Having factories around the world is a must for meeting ever-quickening customer demand, Keane said.
“The market moves so fast. [Manufacturers] make an injection molding machine in four weeks. So you have to produce to meet that cycle or otherwise you don’t get the order,” Keane said.
The next challenge for Nordson is to integrate these acquisitions into a smoothly functioning unit that serves customers worldwide.
“The focus right now is really internal: Taking these acquisitions and stitching them into a single business unit,” said Keane.
Part of that effort is taking place in Shanghai, where by mid-summer the company plans to open a 35,000-square-foot space facility for its 50 sales, operations, engineering and technical staff.
At Chinaplas, Nordson showcased its BKG brand CrystallCut PET pelletizing system, which is being installed in a plant slated to start production this year in Jiangsu province.
“This will be the largest PET plant in the world,” Keane said of the 16-line Jiangyin Chengold Packaging Materials Co. Ltd. facility.
At the facility, the PET pellets will be delivered to solid-state polycondensation systems built by Polymetrix AG of Oberbüren, Switzerland. The spherical pellets created by Nordson’s BKG brand CrystallCut underwater system flow better on a belt than traditional PET strands, Keane said.
“It’s the first underwater PET line in China,” he said.
Nordson also showed off its Xaloy brand liquid silicone rubber package that includes specially designed screw, barrel, seal, valve, and nozzle. Components such as a feed-pipe adapter can be added as needed. The package can be used to manufacture seals, gaskets, cushioning pads, medical devices, infant feeding items, rugged electronic devices and kitchenware.
Nordson’s EDI unit also announced the successful commissioning of the world’s first nine-manifold flat die, which can provide nine-layer film from various resins.
Multi-manifold dies provide much better layer uniformity and thickness adaptation than single-manifold dies. The new nine-manifold die reduces layer thickness variation by about two thirds, from the plus-or-minus 15 percent tolerance often encountered with comparably advanced feedblock systems to plus-or-minus 5 percent, said Sam Iuliano, Nordson EDI chief technologist.
Currently, Nordson Polymer Processing Systems generates about 15 to 20 percent of Nordson’s annual sales. Global sales in the fiscal year ending Oct. 31 were $ 1.69 billion.
In the annual report, the company cited OEMs in emerging nations and the proliferation of lightweight, durable plastics as key drivers of long-term growth.