June 2, 2016 Updated 6/2/2016
Email Print
Christiaan Hetzner
Automotive News
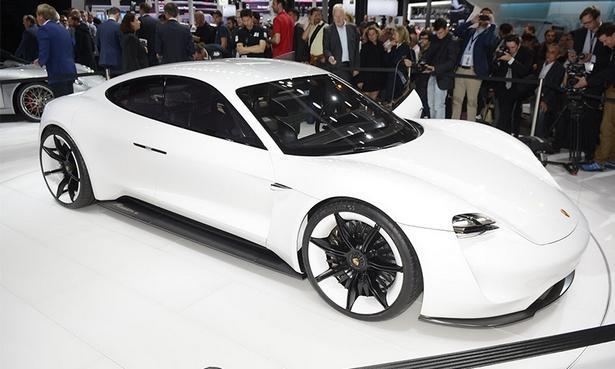
Volkswagen AG Porsche’s Mission E electric is among new electric and plug-in hybrid vehicles planned by VW Group.
Frankfurt — Volkswagen AG is considering building a battery cell plant in Germany that could rival Tesla’s “Gigafactory” as the automaker looks to sell 1 million electric vehicles and plug-in hybrids by 2025.
VW may invest as much as 10 billion euros ($ 11 billion) in the plant, according to press reports.
VW’s finance chief, Frank Witter, said no decisions have been taken on the factory. “We have various scenarios in our strategic discussions and we certainly consider something like that to be a possible outcome,” he said during an earnings call on Tuesday.
Germany’s dpa news agency first reported on the battery cell plant earlier this week, saying a potential location was Salzgitter, 33 miles south of VW’s headquarters in Wolfsburg, Germany. The agency quoted company sources.
VW has estimated that it will have to sell 1 million electrified cars across the group annually, whether battery-powered cars or plug-in hybrid vehicles, by 2025 to meet future increasingly stringent CO2 emission targets in its key markets such as Europe and China.
Individual battery cells use plastic film, while plastics also are used in connectors, frames and may be used as the housing for the battery pack in each car.
By 2020, VW plans to introduce 20 new electric and plug-in hybrid cars including two Tesla fighters — Porsche’s Mission E electric car and the Audi e-tron quattro. Currently, the 12-brand group sells the VW e-Up and e-Golf and the Audi R8 e-tron electric cars, as well as plug-in hybrid versions of the VW Golf and Passat, Audi A3 and Q7, and Porsche Panamera and Cayenne.
With just 12,140 electric Golfs scheduled for production this year, roughly 1 percent of all Golf output, VW needs to make far greater inroads into affordable zero-emission electro-mobility to meet regulatory targets.
‘Critical’ technology
Witter said EV and battery technology was “critical” to VW and that the company was discussing very carefully what was strategically important to manufacture in-house.
He declined to provide further details over the potential amount the group might invest, nor would he say whether the plant would also manufacture the rechargeable cells used for powering electric vehicles. After Daimler closed its Li-Tec cell factory at the end of last year amid a global glut, Germany has lacked a manufacturing plant for one of the most important battery components.
Most automakers assemble their own packs for high-voltage traction batteries needed in electric cars. Those for the e-Golf are made in VW’s factory in Brunswick, Germany while Audi’s e-tron quattro will source batteries from in the same plant in Belgium where the electric vehicle will be built.
Daimler said in March it would invest half a billion euros to double the capacity of its battery pack production site in the former East Germany.
Battery production is expensive, with costs estimated currently at around 200 euros ($ 223) for each of the 40 kilowatt-hours needed to power a conventional electric car. This is in part because many still remain vehicle-specific, a factor that dramatically limits economies of scale.
This could change once dedicated electric cars roll off Volkswagen’s modular MEB platform, a cost-optimized architecture under development for 2019. Engineers say packs will look like tablets of chocolate: essentially flat, portioned into identical units to increase scalability, and flexible in length and width to match the size and range requirements of a particular vehicle.
Tesla has estimated that to meet its 500,000 annual production target in the latter half of this decade, it would use all of today’s available global lithium-ion battery capacity. Its “Gigafactory” currently under construction in Nevada is expected to start manufacturing in 2017 and eventually increase its output to 35 gigawatt-hours of cells and 50 GWh of packs per year by 2020, which will be used to power the brand’s upcoming Model 3 mass-market electric car.
To limit the financial risks, Tesla is splitting the investment with Japan’s Panasonic, which will supply the cells that Tesla then assembles into finished packs.