July 1, 2016
Email Print
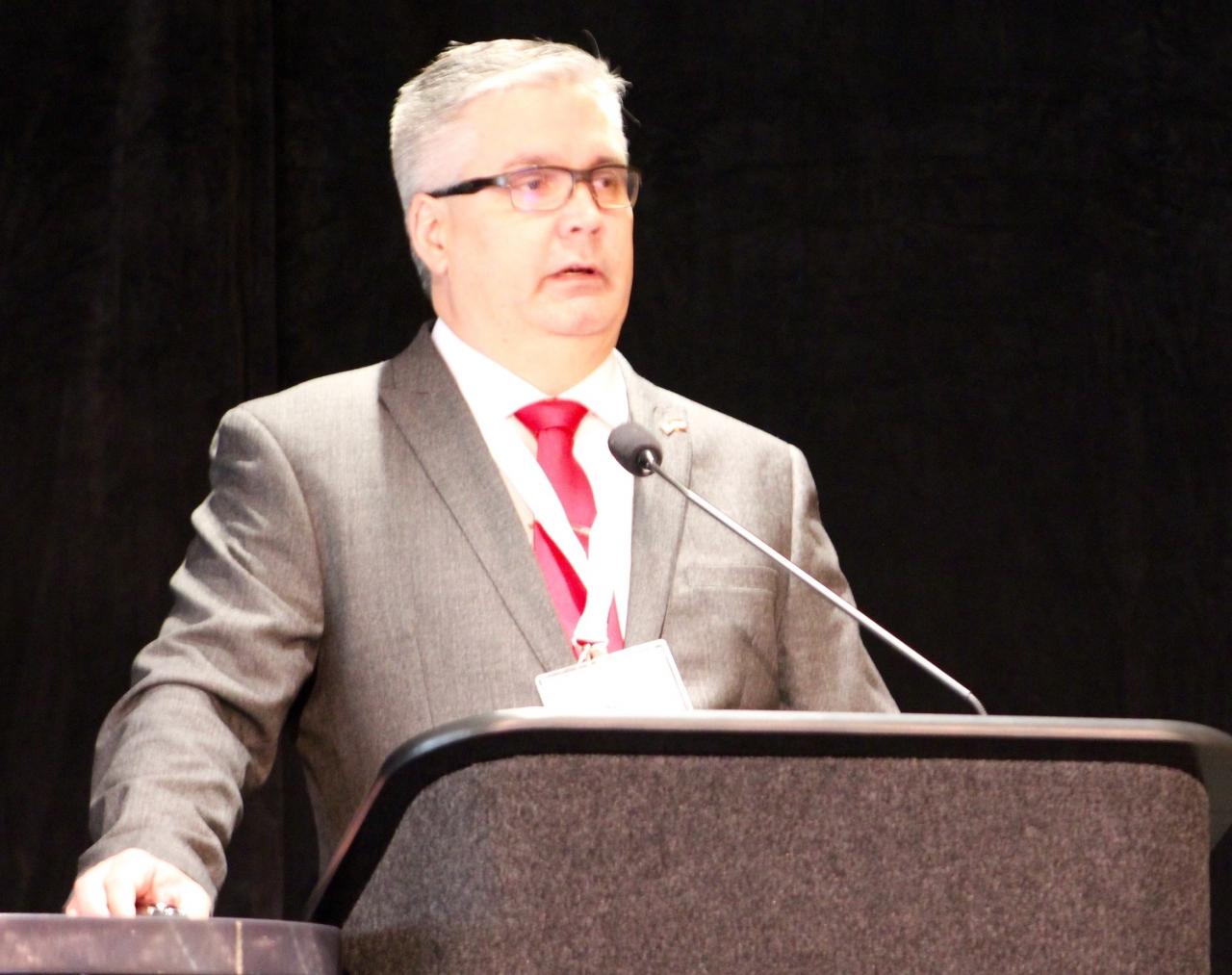
Chris Sweeney, Rubber & Plastics News Pelletier
Akron, Ohio — Robert Pelletier, an expert on dispensing of liquid silicone rubber, dispensed some advice on the closed-loop control of additives for the process, in a presentation at the International Silicone Conference in Akron.
Before jumping into the technical explanations, Pelletier, who does technical sales of dosing systems for Elmet North America Inc., explained that LSR has been more secretive than the plastics industry. “We don’t have the training books in LSR that we do in plastics. Everybody has kind of kept their advances to themselves,” he said.
LSR blends two components, and molders also can use a third dosing system to add color and other materials. Pelletier said Elmet’s latest dosing systems give detailed flow data, using inline pressure sensors and linear transducers, so you know exactly what is happening to the components. The system also tells when material is running out, and the status of drums of the liquid material.
Control of the process is important. “It’s critical that the volume of material goes into the mold at the same pressures each time,” Pelletier said. Correct static mixing also is key. “You have to get consistency from shot to shot,” he said.
Pelletier said closed-loop additive control is crucial, so you don’t waste material or make out-of-spec parts. One key is maintaining the compressibility of the additive, as it goes through the LSR feeding and molding process.
Adding color can be difficult with LSR, Pelletier said. It requires very precise dosing, as well as the correct material size to go through the injection nozzle correctly, he added.
But color is not the only additive for LSR. One example: wearable medical devices, such as cosmetic eye patches. These and other drug-eluting devices require very strict process controls. Pelletier said.
“It’s always good to know how much you’re putting in, how much is left in the system, and how you control it better,” he said.
Elmet North America is in Lansing, Mich.