July 19, 2016 Updated 7/19/2016
Email Print
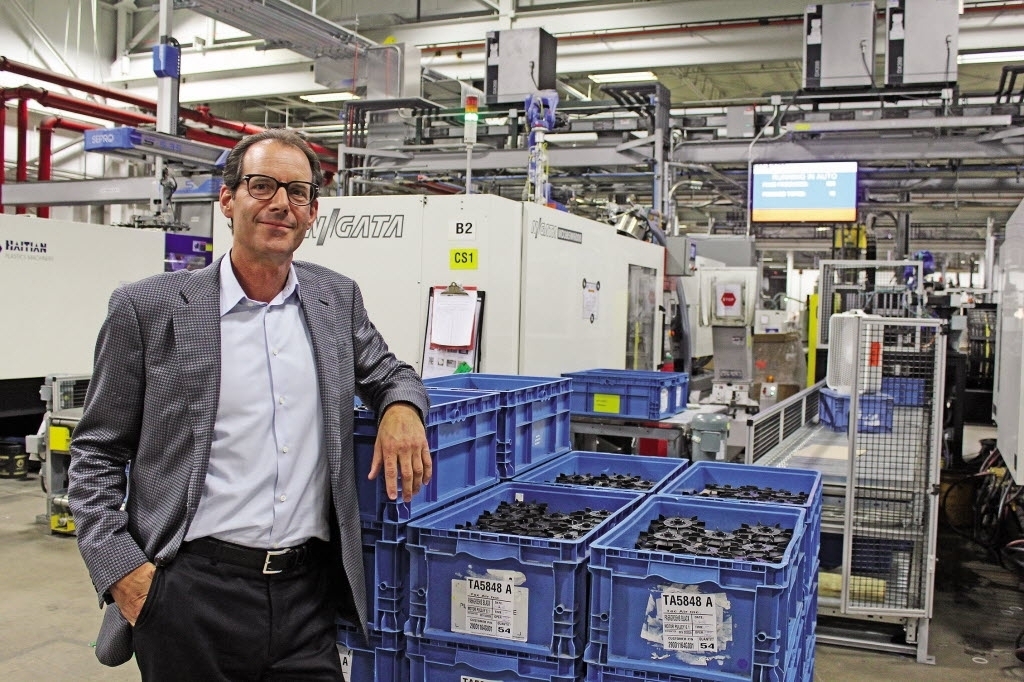
Jeremy Carroll Bob McMurtry, president and CEO of Tec Air Inc. The company crossed state lines for its new location in Munster, Ind., and tripled its manufacturing space.
Munster, Ind. — It’s 26 miles from Willow Springs, Ill., to Munster. A short drive, unless you are moving an entire company.
But that’s exactly what Tec Air Inc. did last fall when the injection molder crossed state lines, tripling its manufacturing space to 130,000 square feet.
Amazingly, the company kept manufacturing during a 10-day transition.
“We never stopped producing, but we did have some slow down,” President and CEO Bob McMurtry said. He pegged the cost of the move and major upgrades to the new facility at $ 15 million.
Tec Air is heavily involved in the automotive and appliance markets, which combine to make up 95 percent of the company’s $ 28 million in sales. Specifically, Tec Air produces dynamically moving air movement devices (i.e. plastic fans and blowers) for those sectors. The company counts many Fortune 500 companies (think GE, Maytag, auto OEMs and Tier 1 suppliers) on its roster of clients.
“We ship products all over the world,” McMurtry said.
The company is built for growth. Tec Air hired consultants and researched open office designs, and included many writable surfaces. Also, many of the office work stations in the new Munster facility sit empty by design. McMurtry said the company has been growing at a 20 to 30 percent clip annually. The new space allows for Tec Air to grow by 200 percent.
Expansion is coming. Tec Air has three manufacturing bays and three cranes with room for a fourth. The company has 42 injection molding machines, including five all-electric, high-efficiency units. McMurtry said Tec Air has spent $ 5 million on capital equipment recently.
The company is hiring quality and processing engineers, a quality manager, process technicians and could add to the sales team in the near future.
“We’re looking for team players who share our vision of continuous improvement. Our one goal is customer satisfaction,” said McMurtry, 59.
His father-in-law, Richard Swin Sr., started Tec Air in 1965. McMurtry describes 93-year-old Swin, who lives in Chicago, as a classic American success story.
Swin sold motors. He thought he could increase sales if the motors’ metal fan blades were replaced with plastic ones, improving the aerodynamics and lessening the weight to gain efficiency. He hired a molder to make the parts, but soon had customers complaining about imbalance and vibration issues.
Like any good inventor, he took matters into his own hands and began making the products himself. Swin eventually secured two patents for in-mold balancing.
“It did work and it revolutionized our business. We still use it in every product to this day,” said McMurtry, an electrical engineering graduate from Northern Illinois University with a law degree from the University of Texas.
Technology and innovation continue to drive Tec Air, 51 years after its founding.
“We put a ton of effort into designing this facility to have new technology and to be highly productive and efficient, to help solve customers’ challenges,” he said, highlighting that Tec Air offers full product design, mold flow analysis, 3-D printing and the ability to easily share data from the manufacturing floor with customers and suppliers through a 200-mega bandwidth fiber-optic connection.
Speaking of connected, McMurtry tells the story of a Tec Air engineer on vacation this month who logged into the system and notified his team via email that one of the company’s robots displayed an error code during third shift.
“That is an amazing change in production management because in our business, in injection molding, it’s a 24-hours-per-day, seven-days-per-week business,” he said.
With its emphasis on innovation, McMurtry is always looking ahead.
“What keeps me up at night is trying to understand what the next technology is. What is the next innovation either in equipment, materials, processes that will allow us to have that jump beyond the competitors.
“There isn’t a huge change in injection molding in the last 30-40 years. The process of plasticizing plastic pellets and squirting them into a mold and taking plastic parts out has not changed significantly. The machine technology to do that, the mold technology to do that, the materials, have changed,” McMurtry said.
“So that’s where the constant innovation is,” he said, adding that Tec Air is evaluating 3-D technology, metal molding, rubber molding, nanotechnology and more so it can offer customers solutions that they haven’t thought of yet.