August 4, 2016 Updated 8/4/2016
Email Print
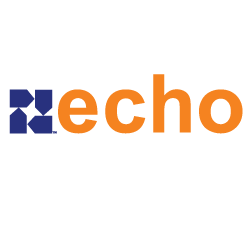
Officials are blowing out 50 candles this year at Echo Engineering and Production Supplies Inc., an Indianapolis-based supplier of engineered plastic and rubber components, caps, plugs and other products used to mask areas of parts during painting and coating.
Echo is celebrating its 50th birthday this year — all of it as a family-owned business.
John Offenbacker started Echo in 1966 in his garage in San Jose, Calif.
“The company started doing work for companies that do design and assembly of printed circuit boards for the electronic industry,” said Kingdon Offenbacker, John’s son, who is Echo’s CEO.
The company sold production supplies to the circuit board sector. Echo got ranked as one of the fastest-growing, privately held companies in the Silicon Valley.
Fast-forward to today, and Echo has offices in Indianapolis and Milpitas, Calif., and provides thousands of plastics and rubber components for a wide range of industries, including automotive, agricultural and fluid power. That part of the business is called direct end-use products — and it can be highly customized.
Kingdon Offenbacker joined the family company in 1992 after college. At the time, Echo was still selling mainly to Silicon Valley, with a smaller amount of business in the Midwest. The company decided to expand its offerings to general manufacturing, setting up an office in Indianapolis.
Echo used to mold its products in-house, mainly smaller parts at relatively low volumes. But as the business grew, starting about 15 years ago, the company partnered with molders in China.
Company officials spent a lot of time in China, and have set up manufacturing agreements with about half a dozen plants there.
Echo works closely with customers to design parts, and can do reverse engineering or manufacture from prints. Often the company uses 3-D printing for rapid prototyping.
Echo makes a large number of grommets, seals, gaskets, mounting clips and many other products. The parts look basic, but Offenbacker said a lot of engineering goes into them.
Importantly, Echo has a full team of its own engineers in every plant it works with in China, Offenbacker said.
“Our process engineers are over there. We go all the way down to the raw materials,” he said. “We’re ensuring that we’re getting name-brand materials. We have people auditing and checking all the time to make sure we’re giving the customers exactly what they should be getting.”
The key is up-front design, design analysis and engineering. “We’ve been growing 20-plus percent for the last five or six years,” he said.
Echo’s product line has become so diverse, that working with Chinese partners was the answer, according to Offenbacker. If Echo tried to manufacture all its own products, in-house, he said: “We would be so stretched and fragmented in what we’re doing. So we’d rather have our expertise in the design, and understanding what the customer needs and what they want.”
Offenbacker said most of Echo’s customers, including large Tier 1 suppliers, have visited the facilities in China and done performance audits. “So it’s not just us telling them. They literally audit our facilities and we welcome it,” he said. “We’re fully transparent.”
Transportation is the biggest market, Offenbacker said. For example: a hanging mounting clip for a fluid routing line. “We convert a lot of metal to plastic, and that’s on the direct product side,” he said.
That is driven by demands for cost reduction and lightweighting, Offenbacker said. “We really focus on these megatrends,” he said.
Another example: A fully-assembled Lexan polycarbonate housing.
“We’re able to be a one-stop shop” for industries like fluid products, Offenbacker said. Instead of using three or four suppliers, he said, “they can buy one-stop from us.”