August 12, 2016 Updated 8/12/2016
Email Print
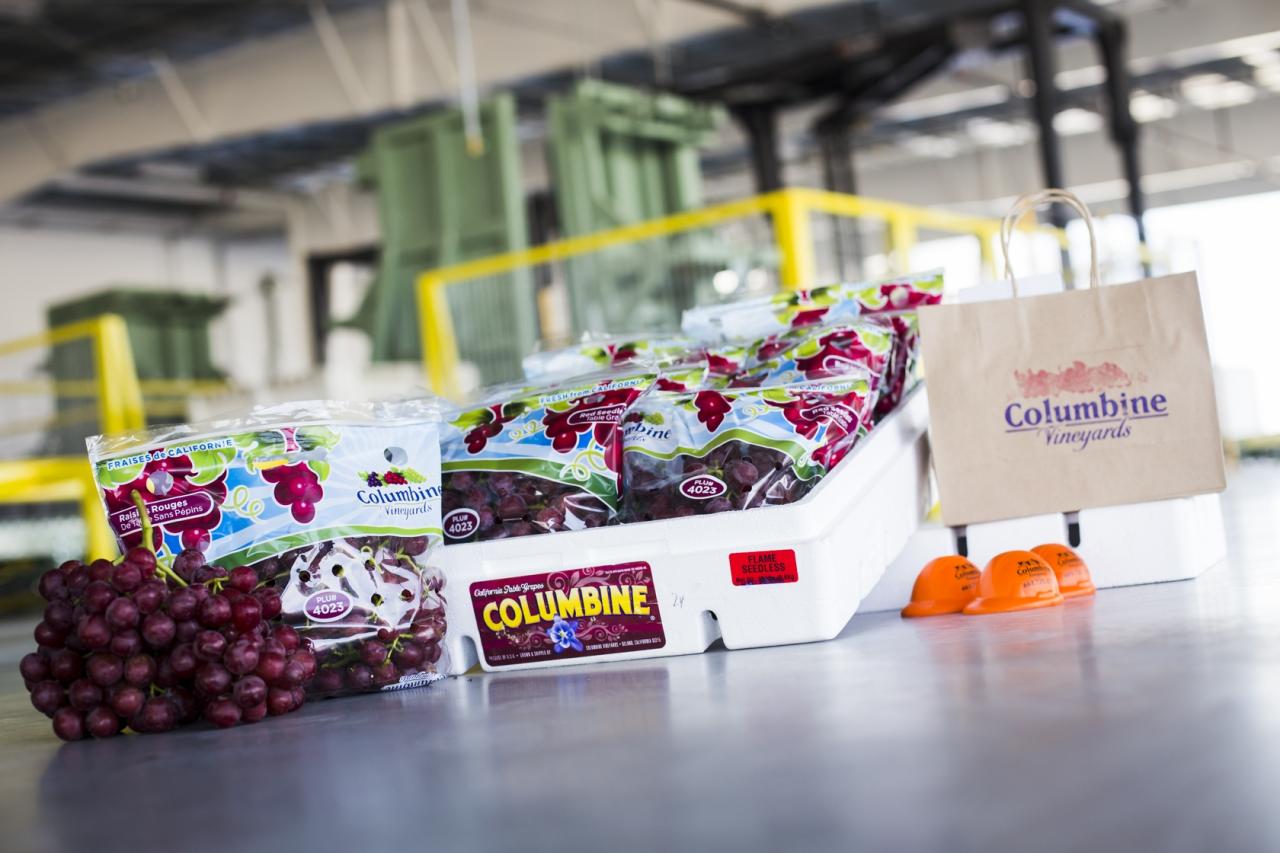
Styrotek Inc. Styrotek Inc. makes expanded polystyrene containers used by California grape growers to both ship and display their products.
There was a time, really not that long ago, that it wasn’t clear Styrotek Inc. was going to survive.
The maker of expanded polystyrene boxes used to ship table grapes around the country and around the world had a troublesome infrastructure that led to inconsistent production and even unexpected shutdowns.
The future was far from certain.
But these days, a little more than a year after CEO Richard Lindenmuth came on board, the company has rebounded thanks to investments that have not only led to improved employee morale but also created excess production capacity that now can lead to company growth.
The Delano, Calif.-based company dates back to 1973 when it was founded by a local grape growers association. Ownership eventually consolidated to the Caratan family, which has been growing grapes in the San Joaquin Valley for 90 years.
“We have actually increased the productivity of the factory by almost 40 percent,” said Lindenmuth, a turnaround specialist who has helped several companies over his more than 30 years in business.
“We were able to put together a system and an infrastructure that uses less water and recycles water, uses less energy and less steam and less natural gas,” Lindenmuth said. “We’re becoming more and more energy efficient. And in doing this, we were able to cut the machine time to produce our products by almost 50 percent.”
Lindenmuth is managing partner for Verto Partners LLC, which bills itself as a corporate strategy, operational improvement and financial advisory firm.
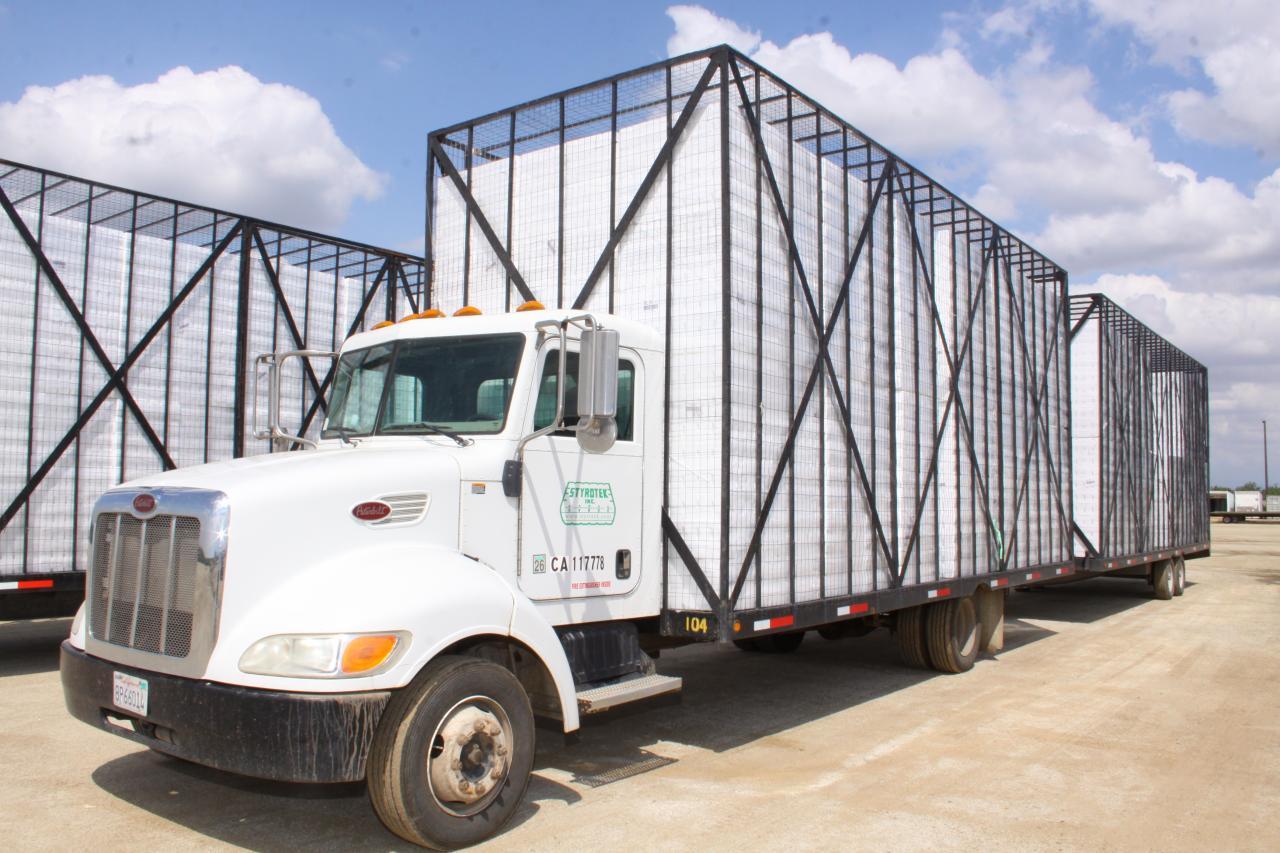
Styrotek Inc. Because foam containers are mostly air, Styrotek has a hedge against shipping from low cost countries.
When he arrived last spring, Styrotek was struggling with a water issue amid California’s severe drought. The state had already shut off the company’s access to water running along a canal right in front of the business in 2014. That was causing major production headaches as Styrotek was forced to rely on water from an old well that was causing boiler problems and disrupting production regularly.
Production Manager Adan Velazquez remembers what he termed a “very troublesome year.
“Everybody was obviously sad, very upset. People were losing their paychecks and going off to find other jobs that they didn’t like as much,” he said.
Production, which was typically 95,000 boxes per day, sometimes fell to 20,000. And some days the machines didn’t run at all.
But that was then, and this is now.
Infrastructure improvements now filter well water to prevent impurities from causing boiler problems. The company also added vacuum pumps to improve product cooling and cycle times. Other additional equipment allows the company to use less steam and get better production results, Velazquez said.
He calls the situation a 180-degree turn for the better. Employees now don’t have to be constantly worried about whether they will have a job.
“We’re seeing people come to work with a different attitude,” the production manager said. “With a teamwork attitude.” Styrotek employees about 130 workers during the busy season.
“The first part was fixing the basic company, which now has been done,” Lindenmuth said. “By fixing productivity, people can see their jobs are steady.
“The next step for us is to include other products. Right now, we’re dependent upon the harvest. If it’s a great harvest, we have a great year. If it’s a bad harvest, we have a not-so-good year,” the CEO said.
That’s why Styrotek wants to talk with other companies interested in using its excess production capacity. That kind of partnership, Lindenmuth said, could benefit both sides.
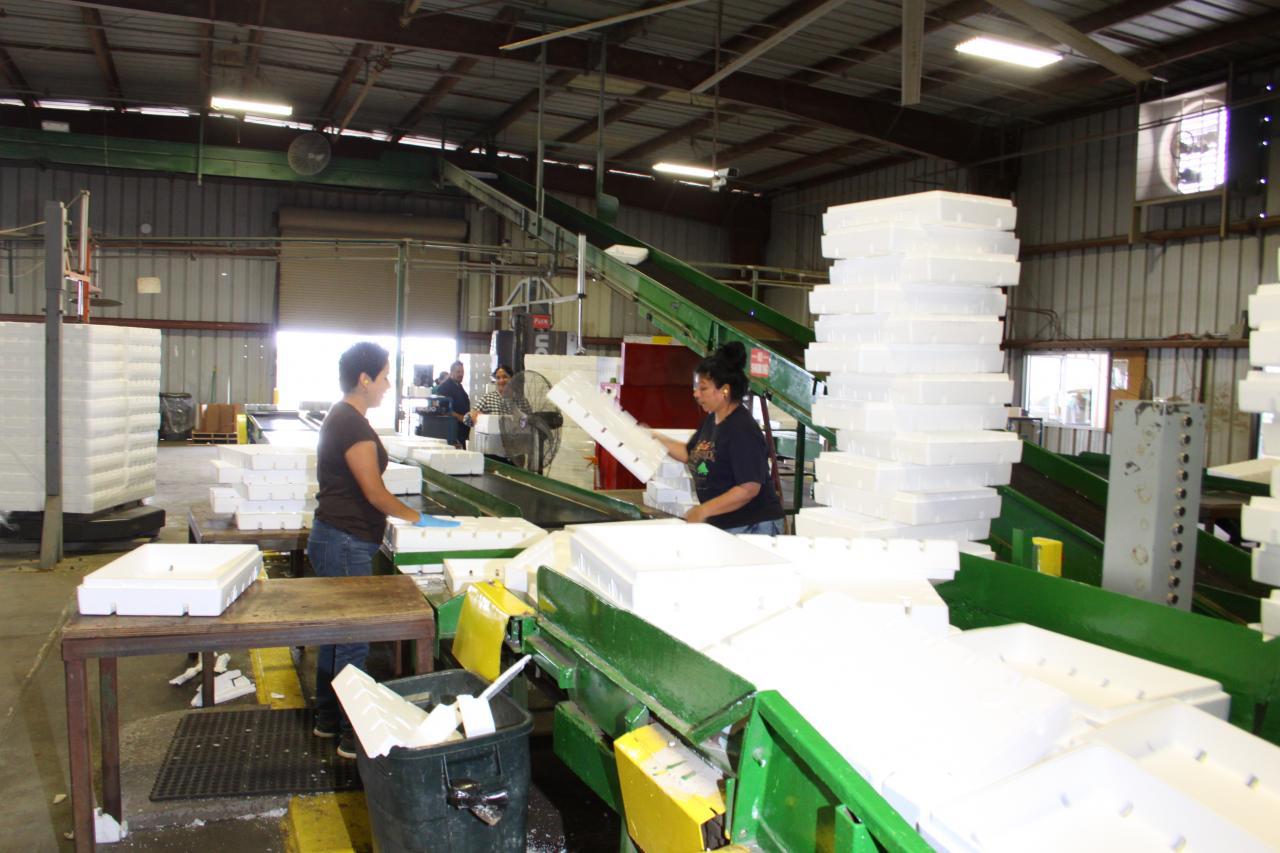
Styrotek Inc. Styrotek typically made 95,000 containers each day.
“If we are able to add some other products from some other people, then all of a sudden we have some more stability and the ability to grow,” he said. And other companies can benefit from Styrotek’s existing infrastructure, lessening their risk and investment.
“We’re now solid and growing,” Lindenmuth said.
Styrotek is bullish on the future of the EPS business, which is finding new applications such as automotive, the CEO said. The company believes the industry will grow substantially in the years to come.
Because EPS is 98 percent air and 2 percent resin, Lindenmuth said his company’s products also enjoy a natural hedge from international competition. “To ship them back and forth from China or from distant marketplaces is not economical,” he said.
Using EPS to package grapes allows them to be refrigerated during distribution and extends shelf life.
Table grapes are a $ 2 billion business out of California, and cold chain storage has about 40 percent of the packaging for those grapes. Styrotek, in turn, has about 50 percent of that cold chain storage packaging market, the company said.
Lindenmuth believes there can be an effective recycling program established for EPS boxes sent to grocery stores via cold chain storage, similar to programs already in place to handle other recyclables such as rigid plastics and film.
A key is to making sure people understand that EPS is recyclable and putting collection and back-hauling systems in place to handle the material. He sees the potential of putting recycling equipment, such as densifiers, in distribution centers to handle all sorts of returned EPS, not just grape boxes.
“There’s a very, very good understanding that green is better and so there is much more motivation than there was three or four years ago, particularly for grocery chains, to be as green as they possibly can,” Lindenmuth said.