August 15, 2016 Updated 8/15/2016
Email Print
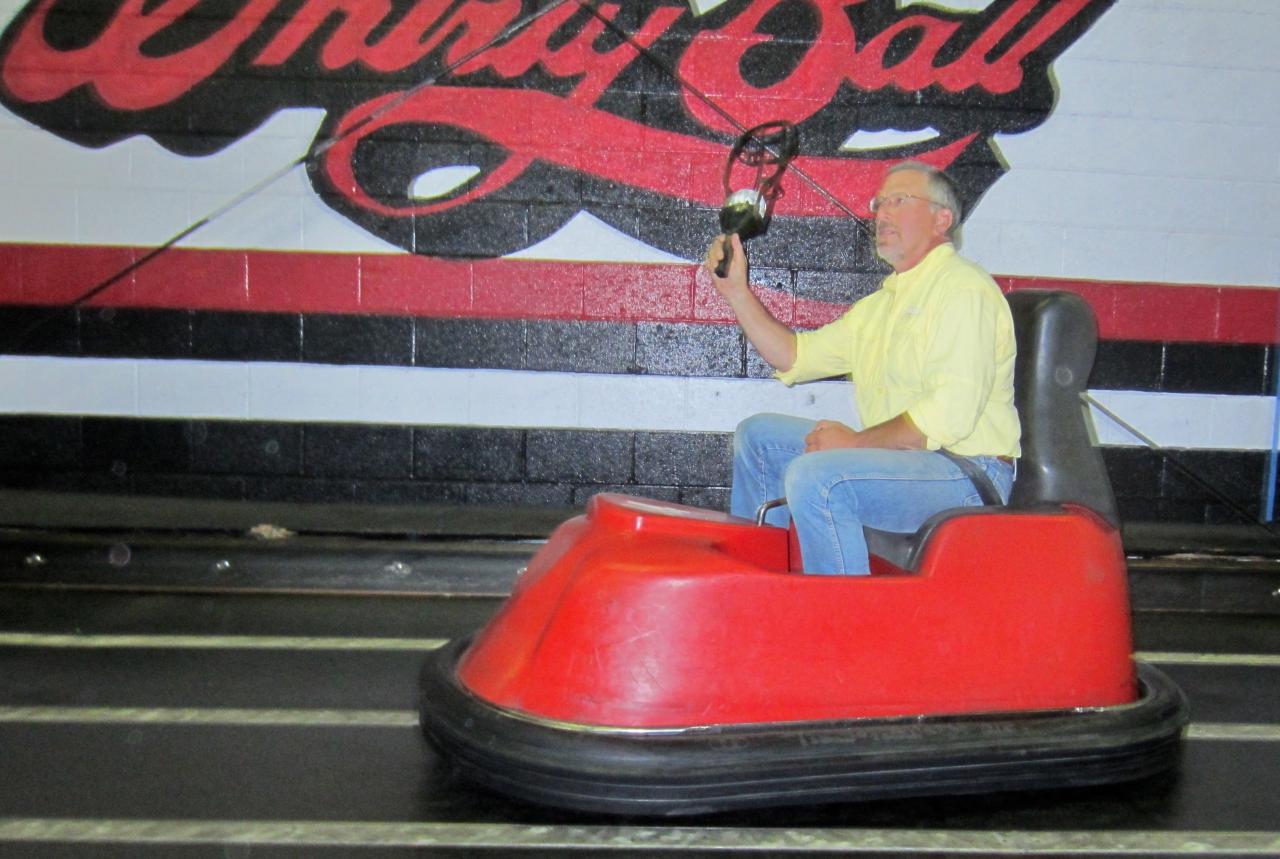
Bill Bregar Rick Englehart’s Englehart Moulding Corp. rotomolded the bodies for WhirlyBall carts, replacing fiberglass models.
Cleveland — Rick Englehart is hanging up his cleats and selling his company, Englehart Moulding Corp., after more than 20 years of rotational molding, specializing in large, challenging parts.
“I’m looking to sell,” he said.
He stopped production at the Cleveland plant about six months ago, after winding down molding work for customers. The company, which had employed between 20 and 40 people over the years, had 12 employees when the plant closed.
Now Englehart is looking to sell the equipment — a large independent-arm Ferry RS3-500 with three arms and a 200-inch swing, and a smaller FSP M-80 with an 88-inch swing. Also for sale: kayak tooling that was the core original business for Englehart Moulding.
Englehart, 55, said he had a great time in the rotomolding business.
“It is time to find a good home for my ovens, pass the torch and take a little me time,” he said. “I’ve half-heartedly been considering retirement for a while, but now it is time.”
But he’s looking for the right buyer.
“I want the customers to be happy with whoever they’re going to be dealing with,” he said. “I’m looking for a home that’ll work it properly so they can take of customers the right way.”
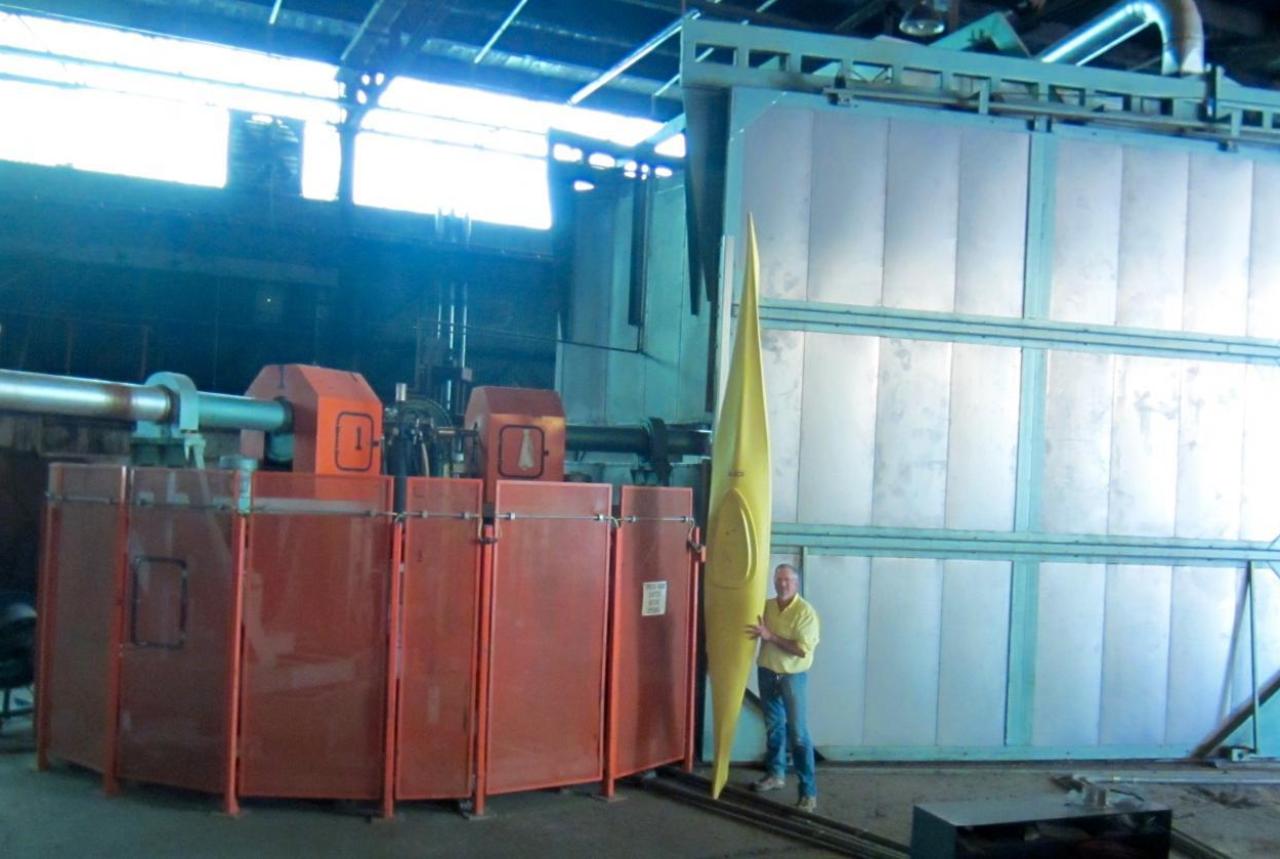
Bill Bregar Englehart at his plant with one of the kayaks made by Englehart Moulding Corp. and one of its massive rotomolding machines.
Englehart loves paddle sports, canoes and kayaking. “I’ve been paddling since I was 18,” he said.
The sport led him to rotomolding. Englehart started out in the late 1980s designing wood canoes and kayaks. He soon saw that children wanted to learn the sport, but had to use full-sized, adult equipment. He looked at composites and other processes before picking rotational molding for the smaller-sized kayaks.
Englehart said he began working with mold makers and other rotomolders starting in 1990 on the boat line, before deciding to start his own molding company in 1995, in Newbury, Ohio. He knew right away he would need the big independent-arm Ferry machines to make the kayaks. Rock-and-roll machines often are used to make kayaks, but Englehart said that process is slower and it limits the shapes of kayaks.
The Ferry RS3-500 requires a clear space of 52 inches for the arms, and a 25-foot-high ceiling.
The operation outgrew the first plant, then moved to Euclid, Ohio, and for the last 16 years has been in Cleveland.
Englehart expanded into custom molding, focusing on difficult parts. For General Dynamics, the company molded 14-foot-long gas tanks for a Marines amphibious assault vehicle. For the Lawrence Livermore National Laboratory, the company molded a polycarbonate frame used to grow crystals at the National Ignition Facility.
Other customers included DaimlerChrysler and Little Tikes Commercial Play Systems… and WhirlyBall.
One happy customer is Rick Morad, president of WhirlyBall Cleveland. Unsatisfied with the old fiberglass cart bodies, Morad joined with two other WhirlyBall centers and got a rotational mold built. Several rotomolders tried to produce the shell body, without success, until the mold maker suggested trying Englehart Moulding.
Morad said Rick Englehart’s company molded about 150 of the carts. “Since then, he’s become a friend. He, in two weeks, gave me a prototype better than anything I had before,” Morad said.
The cart bodies are durable, but when they do need to be replaced, Morad said he will miss dealing with Englehart Moulding.
“Wherever I land, Rick is going in there and telling them how to do it,” he said, chuckling.