August 29, 2016 Updated 8/29/2016
Email Print
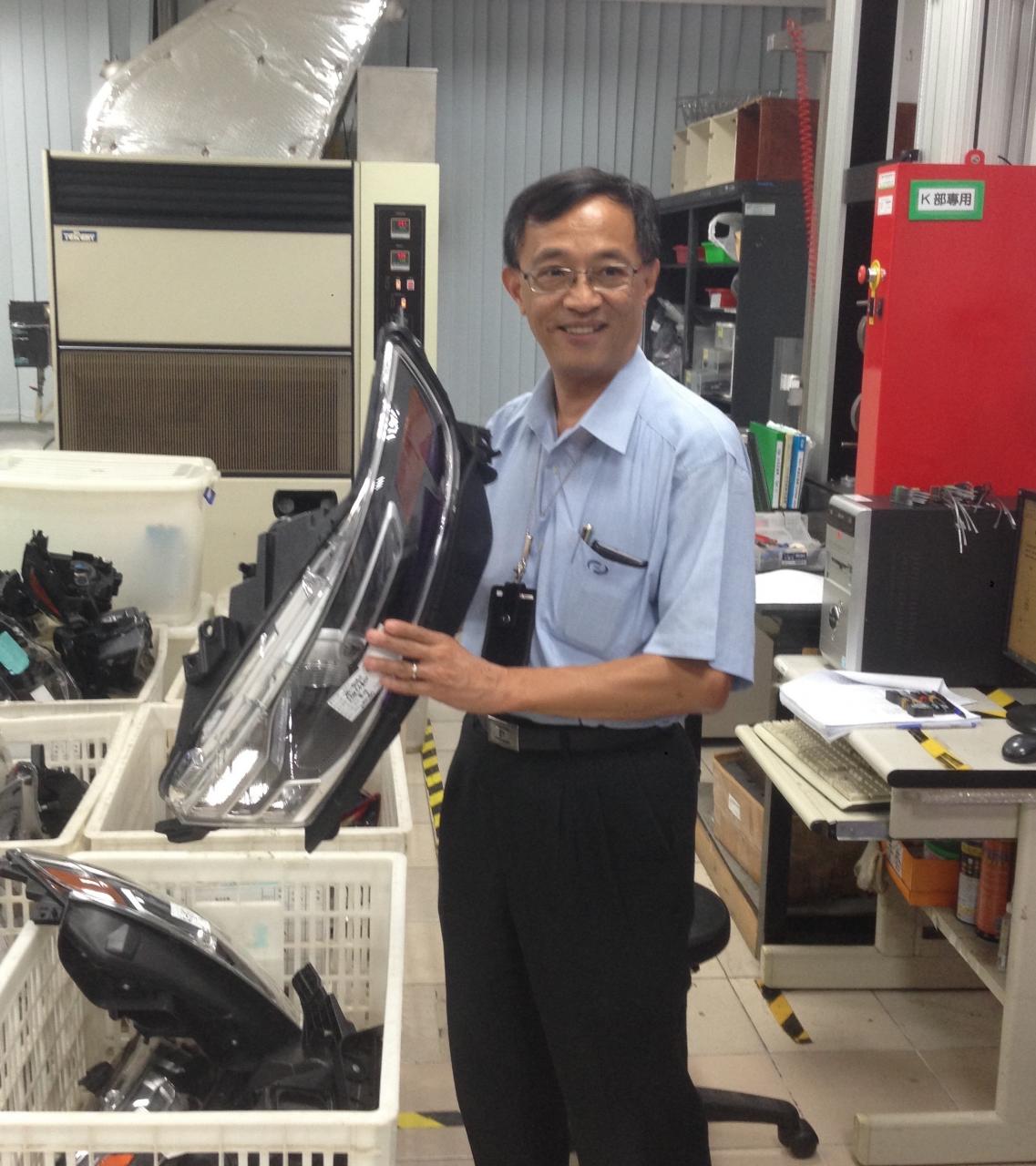
Kent Miller Zen-Wen Chiou, vice president of the Plastics Industry Development Center.
Taichung, Taiwan — Construction is forging ahead on $ 10 million medical polymer research center that’s the latest sign of Taiwan’s determination to target the upscale plastics market.
While China and Southeast Asia will continue to churn out commodity products, Taiwanese processors can focus on high-end offerings like medical devices and lightweight car parts.
“We don’t make regular plastic bags and water buckets, things like that. They’re too low value. So we go for high value-added items,” said Zen-Wen Chiou, vice president of the Plastics Industry Development Center, which is building the new lab.
When it opens in 2018, the lab, a half-block from the main PIDC building in Taichung, central Taiwan, will focus on device design.
“In Taiwan, we still don’t have the capability to design or develop the new polymer materials for medical use,” Chiou said. “Those materials need to pass regulations, and that will take a very long time.”
The center aims to bring together traditional polymer engineers with experts in human anatomy, hospitals and medical regulations from the Taichung area’s hospitals and medical schools.
Private industry will be able to access the center’s pricey equipment, too. “It will be an open laboratory that industry researchers can come and use,” Chiou said.
PIDC eschews the theoretical approach of Germany’s famed Institute of Plastics Processing (IKV) at RWTH Aachen University. Instead, the more pragmatic approach here is to work on products that can ship to market in a few years.
Currently, thermoplastics for automotive and aerospace applications are key areas of research. Aerospace, especially, is a high priority for Taiwan’s president, Tsai Ing-wen, who took office in May.
“That’s created a lot of opportunities for plastics applications, especially fiber reinforced composites and advanced materials,” said Chiou.
The center works with injection molding machine maker Victor Taichung Precision Machinery Works Co. Ltd. to make screws optimized for long-fiber — more than 12 millimeter long — composites.
PIDC is also researching advanced films. One humble but practical innovation was a plastic bag that extends the shelf life of fruits like bananas that emit ethylene gas, Chiou said.
“We’ve had a lot of success with our agricultural applications,” Chiou said.
From its inception in 1992, the PIDC has focused on serving the small- and medium-sized that make up the vast majority of the island’s plastics enterprises. The nation of 23 million has more than a million small businesses — a tribute a strong entrepreneurial ethos, but a challenge when it comes to staying on top of cutting-edge technologies.
“They can’t do much research. They are too small. This is one of our missions: to help the medium and small-scale companies,” Chiou said.
Smallness can be great, but it also means that means that the industry needs to work hard on implementing Industry 4.0. “If you look close enough at [the Taiwanese industry’s] machines, the whole facilities and style of manufacturing, probably it can be categorized Industry 2.5. so we haven’t reached 3.0 yet.”
The PIDC, which Chiou dubs a “semi-non-governmental organization,” gets its $ 13 million annual budget from a 50-50 mix of public and private resources. Besides research, the company offers a gamut of small-business-friendly services, including safety and health testing. The center offers a steady stream of seminars and courses throughout the year, including certificates in basic and intermediate injection molding engineering and materials processing. There’s even assistance in advertising and brand licensing.
The medical polymers lab will join Taiwan’s two other research centers for medical devices. One focuses on electrical devices such as CT scans and holograms, while another is developing metal surgical tools.