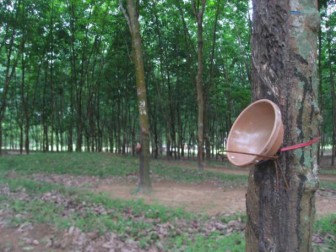
The 6,000-square-foot pilot plant in Wooster makes gloves and a variety of other latex and rubber products. This is nothing new in a town and region historically known for rubber manufacturing. What’s different about the facility is the source of its natural rubber: plants grown in the United States rather than the Southeast Asian trees that currently provide all of the world’s supply of natural rubber.
Established earlier this year, this unique pilot plant is operated by Ohio State University’s Ohio Agricultural Research and Development Center (OARDC). It’s a crucial step in the university’s effort to develop and commercialize domestic natural rubber sources that could one day replace a portion of the imports of this strategic yet largely overlooked raw material.
While led by OARDC, the project — funded by a $3 million Third Frontier grant from the state of Ohio — also involves the U.S. Department of Agriculture, the University of Akron and Oregon State University. Industry partners include Bridgestone, Cooper Tire, Veyance Technologies and Ford Motor Co.
“Natural rubber is probably the most underappreciated critical resource that we have,” said Katrina Cornish, project leader and OARDC endowed chair in bioemergent materials. “There are over 40,000 things made with natural rubber, including 400 medical devices. Life as we know it wouldn’t be possible without natural rubber.”
Driving to the grocery store wouldn’t be possible. Neither would be flying around the world. Even with the most sophisticated advances in synthetic rubber technology, passenger vehicle tires need about 50 percent natural rubber content to adequately resist the road’s demands, said Hiroshi Mouri, president of Bridgestone Americas Center for Research & Technology in Akron.
And in the case of aircraft tires, they are made entirely from natural rubber.
“It’s very important to have an alternate source of natural rubber,” said Mouri, who works closely with OARDC in the project. “We want to diversify the sources of natural rubber to make sure our production is sustainable. The rubber tree has a history of extinction in the past in Brazil, and if that happens in Southeast Asia, we won’t have a source of natural rubber. So it’s important to have other alternatives.” Those alternatives include Taraxacum kok-saghyz, or TKS — a type of dandelion native to the former Soviet republics of Kazakhstan and Uzbekistan. This plant can produce large amounts of rubber in its roots and can grow in Ohio and other temperate areas of North America. OARDC researchers have been working for the past six years on turning this weed into a crop that can grow on a consistent, predictable basis and can yield as much rubber as possible.
Guayule potential
The second plant being researched at OARDC is guayule, a shrub native to the southwestern U.S. that produces rubber safe for latex allergy sufferers. Cornish is a national expert on guayule, having served as senior vice president of research and development for Yulex, a company founded to commercialize the technology she developed while working for 15 years in the area of domestic rubber crop development with the U.S. Department of Agriculture. Cornish and other Ohio State researchers are conducting trials in southern Ohio to test the adaptability of guayule to the region.
OARDC’s pilot plant now allows researchers to produce rubber samples from these plants that are large enough for industry testing. In the case of TKS, this is accomplished thanks to rubber-extraction equipment based on a process initially devised during World War II (when the U.S. first studied TKS), and which has been refined and further developed by OARDC biosystems engineer Fred Michel.
The pilot plant can produce compression-molded and dipped products, such as medical gloves; macro, micro and nano fillers, which are used in a variety of industrial products as reinforcement; and filled latex and rubber test samples. OARDC conducts latex and some rubber testing, while polymer science experts at the University of Akron carry out additional rubber testing to see if the samples meet industry standards.
So far, the results are favorable.
“Our recent studies continue to indicate that TKS has the potential to produce similar properties to Asia-produced rubber,” said Mouri, whose team at Bridgestone has also developed prototype tires made from guayule rubber. “We work very closely with Ohio State because we don’t have expertise in plant breeding and agricultural research. Our expertise is in evaluating if the rubber is suitable for tire applications. So we make a good combination.”
Making a new crop
While guayule has been the subject of significant research and commercialization in the past, TKS is just now in the process of crop development, said Matt Kleinhenz, who leads the TKS breeding and agronomy program at OARDC.
This process started in 2006 with a small number of TKS seed collected in the wild. Roots of those plants contained 1.2 percent rubber on average. Growing in greenhouses, in high tunnels and in open fields, those seeds been crossed over the past few years, generating groups of plants that are continuously evaluated for characteristics such as growth rate, root structure and, of course, rubber yield. This year, Kleinhenz’s research team produced close to 13 million TKS seeds from plants containing nearly 9 percent rubber on average.
These seeds are a unique collection that researchers hope will become the foundation for TKS as a crop.
So far, plants with roots containing up to 20 percent rubber have been developed, Kleinhenz said. By comparison, the common dandelion, Taraxacum officinale, produces little to no usable rubber. TKS has been planted and harvested in both spring and fall. Either way, the cold of winter appears to help to increase rubber content, he explained. Also, the plant requires few agricultural inputs, increasing its potential as a cash crop.
“It’s rare to have the opportunity to develop a new crop from scratch,” Kleinhenz said. “It’s complex and requires a lot of work.
“But when we succeed, TKS will provide farmers in Ohio and beyond with another option to add to their crop rotations and make money. It will also generate jobs and additional economic activity from transportation, equipment manufacturing, processing and other activities in the supply chain.”
TKS roots also contain inulin, a carbohydrate used as an additive in foods such as yogurt and which can also be converted to fuels such as ethanol and butanol.
More research still lies ahead to breed a plant with the right combination of agronomic characteristics that would make a suitable crop for farmers to grow. Other considerations, such as seeding rate per acre, are being worked out as well. Researchers are also looking for the most effective way to control weeds in TKS stands, since cultivation is out of the question because the plants lay too close to the ground.
“TKS is not going to survive as a crop without effective weed control,” said John Cardina, an OARDC weed expert. “This plant is not very aggressive. As a weed, it’s actually a bit of a wimp.
“It doesn’t grow fast and doesn’t cover much ground, which means weeds can take up a lot of room quickly, taking away light availability, nutrients and water from TKS. Chemical control is our best option, but there’s the challenge that TKS is closely related to things we now treat as weeds and that available herbicides kill.”
Cardina has tested a variety of herbicides and found three post-emergent products that look like good candidates. These are herbicides currently used in crops closely related to TKS, such as lettuce and sunflowers. He said he hopes to have a package of weed management options ready next year, after running additional experiments.
Rubber economics
The importance of developing alternative sources of natural rubber becomes clear when considering that there has been a shortage in the supply of this critical resource every year since 2004, said Bryan Kinnamon, Industry Liaison Office director for Ohio State’s College of Food, Agricultural, and Environmental Sciences — which includes OARDC. Rapidly increasing demand from emerging economies such as China and India is behind the shortage.
This situation has led to supply uncertainty and price volatility, which affect industries dependent on natural rubber. And things are expected to get worse.
“By 2020, the global shortfall of natural rubber is projected to be more than the entire amount (1.2 million metric tons) the U.S. imports every year,” Cornish said.
More information about the natural rubber project is available at http://www.oardc.osu.edu/penra/.
Source: equities.com