November 17, 2015 Updated 11/18/2015
Email Print
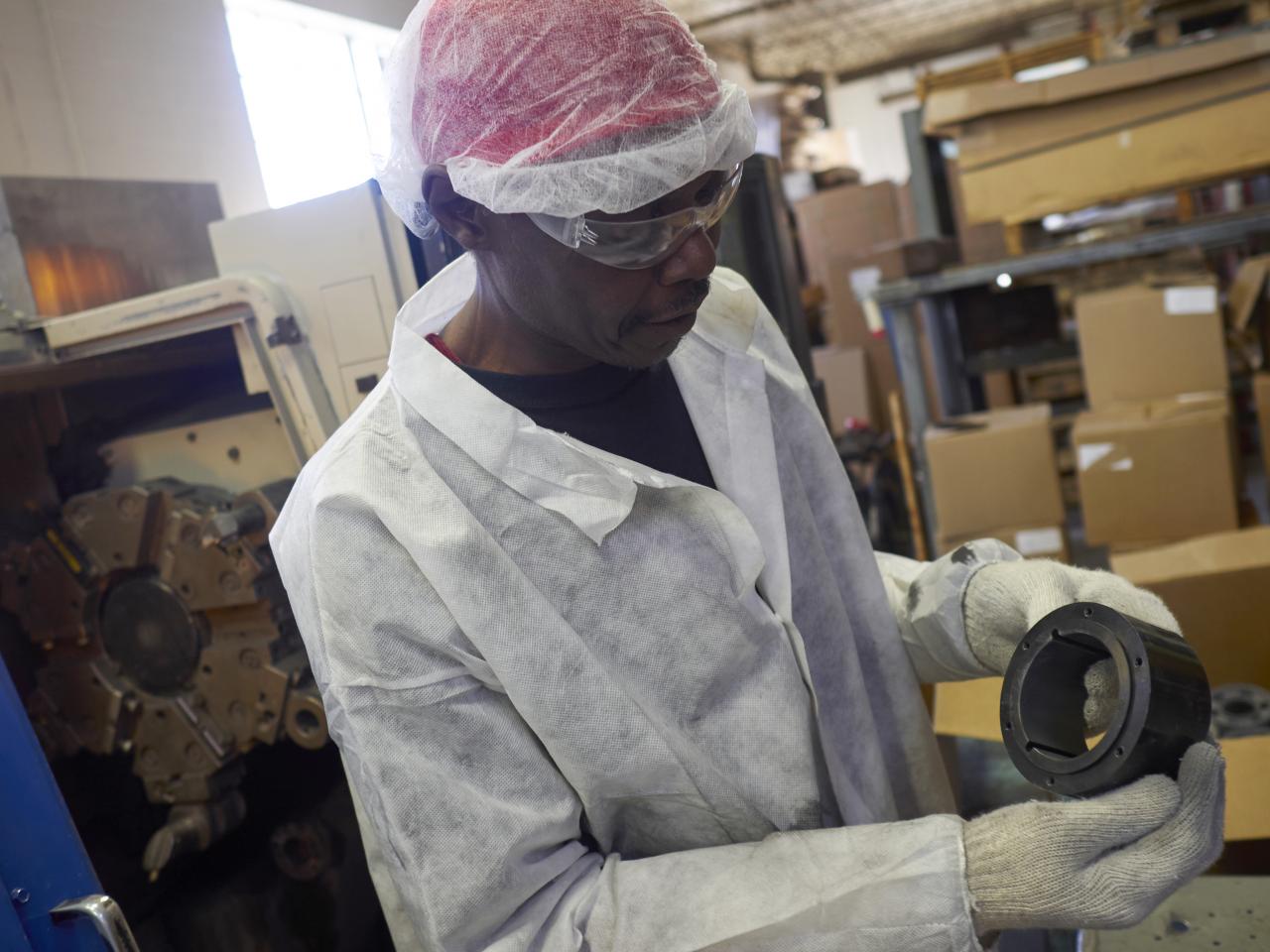
Cornerstone Composites Inc. Cornerstone Composites Inc. has found a niche producing phenolic molded hubs for reel-to-reel institutional and commercial recording tapes.
Recently formed thermoset specialist Cornerstone Composites Inc. has entered the legacy business of reel-to-reel tape components.
Cornerstone, created by the merger of Wisconsin Thermoset Molding Inc. and Rose Polymer Composites LLC, bought the goodwill and technology of AcroReels and is molding components for a storage medium that persists in the era of digitization.
The AcroReels acquisition in April launched Cornerstone into molding phenolic resin into hubs used in commercial and institutional tape deck reels. Like proponents of vinyl records, some commercial tape deck users are sticking with the technology when everything around them is converting to compact discs and other electronic storage systems. They might like the different “feel” of analog magnetic tape and the ease of editing through tape splicing.
“We like the reel hub business because it is highly engineered,” explained Andy Stroh, Cornerstone vice president of sales, in a phone interview. The company now molds precise hubs that fit stamped aluminum flanges to make reels to hold PET recording tape about 1 to 2 inches wide. Such tapes are still used in high-end audio recording studios, to record movies and to store data for governments that don’t want to transcribe all their historical data to a new medium such as compact discs.
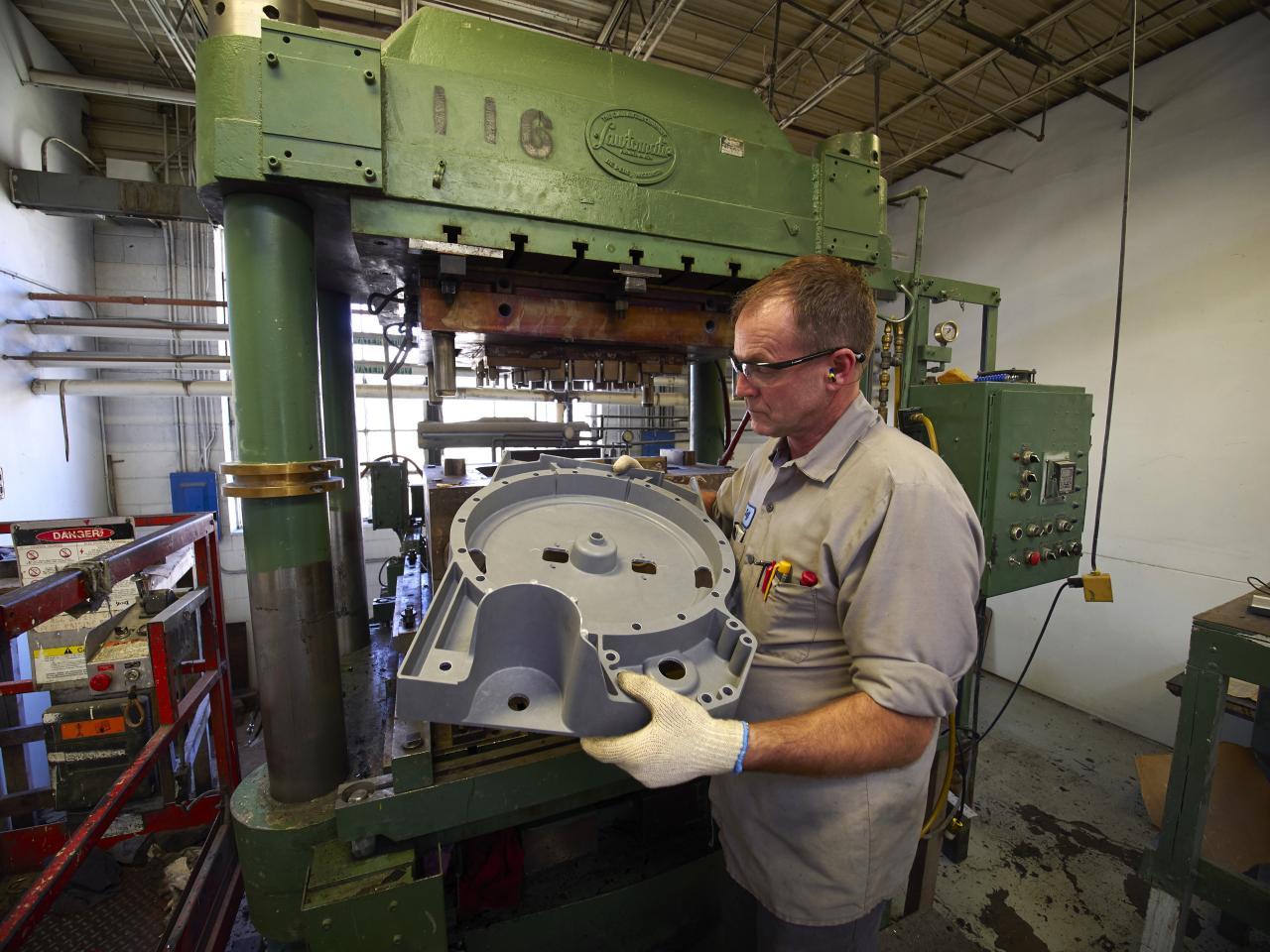
Cornerstone Composites Inc. High-voltage device components are molded from thermosets by Cornerstone.
Stroh said his firm’s market has few players since it is a legacy niche. Cornerstone molds phenolic hubs for commercial reels that compete with all-metal reels in a market of some thousands of reels annually. The plastic/metal reels do not compete with low-end technology reels used in the tiny market for consumer applications such as quarter-inch magnetic tape.
Stroh said the phenolic hubs need to be dimensionally stable to meet magnetic tape recording specifications. Producing hubs by chopping a thermoplastic tube doesn’t give the high quality recording hardware that engineers demand.
Cornerstone is promoting thermoset molding as a valuable tool for OEMs looking for more effective ways to make components. Stroh said it ranks with 3-D printing and automation in the thrust to replace metal parts with plastic ones based on plastics’ lighter weight, corrosion resistance and productivity. High-voltage devices are another kind of tough, engineered product Cornerstone focuses on.
“We look for applications beyond the reach of thermoplastics,” Stroh stressed.
Cornerstone was born after the two Milwaukee thermoset molders merged in January. The new business runs 32 presses with clamping forces up to 600 tons for compression molding, injection molding and resin transfer/compression molding.