January 22, 2016 Updated 1/22/2016
Email Print
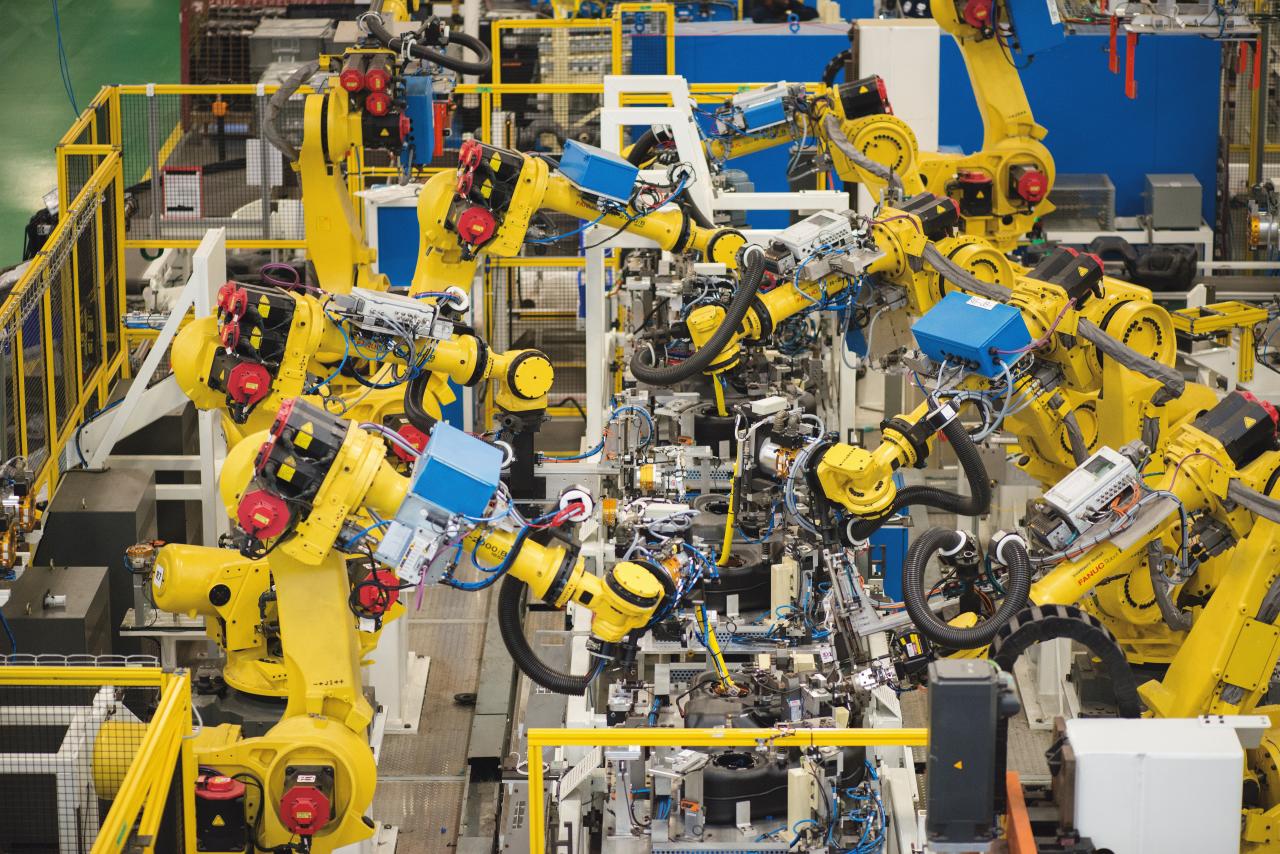
Cie. Plastic Omnium Production of fuel tanks at a Plastic Omnium plant. The auto supplier also makes bumper fascia and front and rear end modules.
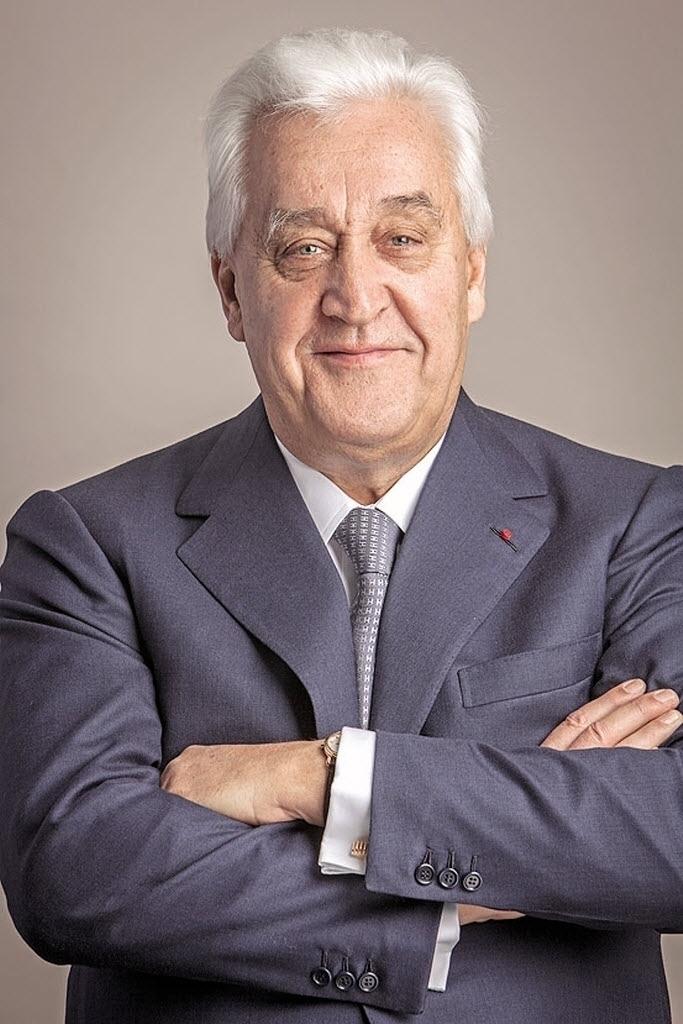
File photo Burelle
Detroit — Cie. Plastic Omnium has been a key player in the automotive plastics arena for more than 40 years.
It was a supplier when the first plastic bumpers came on the market in 1975. It was the first global supplier of plastic fuel tanks in 1984.
And it is building a technology and global footprint that will ensure it remains at the center of the auto industry, whatever future cars may look like or how they are driven.
“As far as [millennials] are concerned, a company like ours that makes things is dead. But they need us. That’s the good news,” said Laurent Burelle, chairman and CEO of Plastic Omnium, in a Jan. 11 interview at the North American International Auto Show in Detroit. “They will need something to bolt on their stuff — their sensors, their radars, their cameras, their whatever. They will need to have a body — a box — to safely transport them from point A to point B.
“If the [powertrain] is hydrogen, if it is gasoline, if it is electrical, whatever, they will need to have a safe body — a light, safe body and if possible one that is colorful and sexy to attract buyers.”
Late last year, the Cedex, France-based injection molder and blow molder inked a deal to buy the bumper fascia business of Faurecia SA, a deal that will bring it additional production and market share in North America.
For 2015, Plastic Omnium had $ 2 billion in sales in North America and 4,500 employees in the region. It is the 47th biggest global auto supplier now and with the acquisition of Faurecia’s operations, it will grow to 25th.
In 2014, it posted 5.3 billion euros ($ 5.7 billion) in sales globally. With the addition of the Faurecia operations, it said it will have 8 billion euros ($ 8.6 billion) in global sales.
The purchase will bring it one plant in Canada, eight in the United States and 10 in Mexico, supplying injection molded fascia, blow molded tanks and front and rear modules, which include a variety of parts which can integrate lighting, cables and radiators. It also makes diesel treatment systems for trucks.
In total, the company expects to invest $ 450 million in new production in North America in the next five years and another $ 200 million in research and development in the region.
By 2020, it aims to evenly divide its sales with a third of its business in North America, a third in Europe and a third in Asia. Right now, Europe makes up 50 percent of its sales with another 25 percent in North America and 20 percent in Asia with the rest divided between the rest of the world.
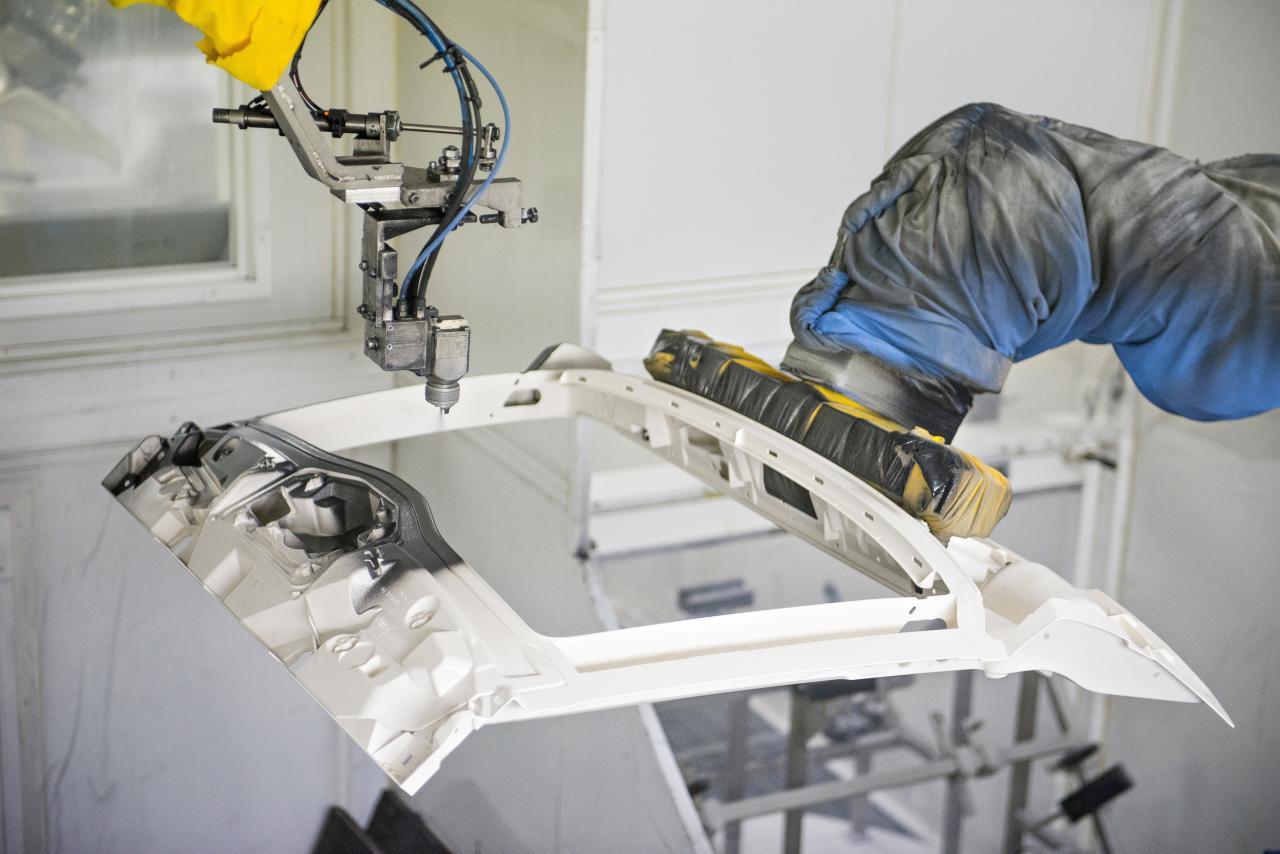
Cie. Plastic Omnium Burelle said he can picture when electronic sensors are embedded in the coating on auto parts.
But Burelle, speaking just a few hours after a press event when Ford Motor Co. executives spent as much time talking about connected vehicles as they did introducing new products, said he can imagine a new auto production supply chain in which a new start-up automaker buys a series of big, plastic modules to build their cars.
“A new [automaker] buyer may be a buyer of bigger parts, maybe more intelligent parts. Are they bigger modules where the car industry will not buy part by part, but purchase complete modules? A front end module, a side module, floor modules, roof modules, rear end modules so, five modules? Then they will just add the different functions they need.”
And plastics may offer something that other materials cannot.
Already, car companies are packaging antennas and sensors in bumpers and spoilers and other exterior plastics because many of those parts are not compatible with metal parts.
“The raw material approach, the chemical approach, it has a role to play,” he said. “It could be electronic everything out there, but chemistry may have something new to say, and that’s exciting.”
Taking the possibilities of plastics and chemistry even further, Burelle points out that researchers are looking at ways to integrate electronics directly in film and coating. Imagine, he said, a paint on a plastic part that also can collect and emit electronic signals.
There have already been sun roofs that integrate solar energy collectors to help regulate a car’s temperature when it’s parked. It may be possible to take that further in the near future.
Plastic Omnium has taken steps to keep Burelle’s vision in that future auto industry in place. On Jan. 1, it named Jean-Michel Szczerba co-CEO. Szczerba has been with the company since 1985 and served as chief operating officer since 2010.
And while both he and Burelle say they have a lot of activities in multiple markets to track — along with new technology and new plants — they are “long term industrialists” who control the majority of capital in the company.
“We like to take the risk of innovation,” Burelle said. “To innovate is to accept that you may fail, but if you don’t accept that you could fail you don’t innovation. An innovation may turn out to be worth nothing and that means you have to write it off. But if you are not ready to lose, then you don’t play.”
Laurent Burelle talks about Plastic Omnium’s plans in North America in this Plastics News Now report from the North American International Auto Show.