June 16, 2016 Updated 6/16/2016
Email Print
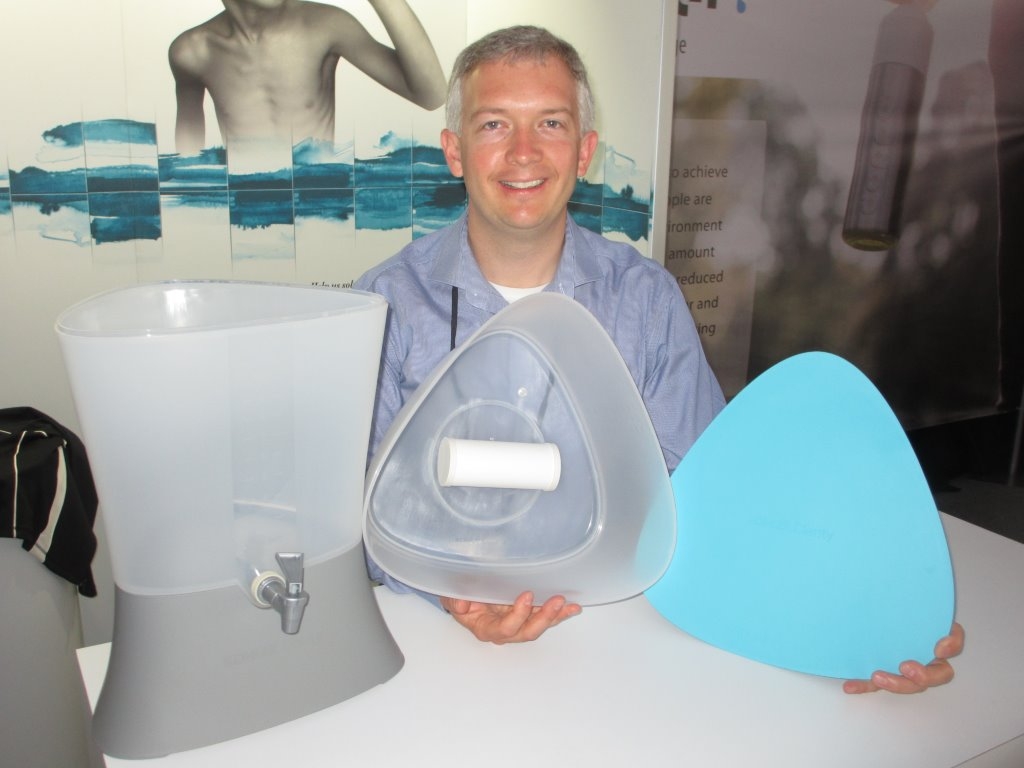
Roger Renstrom Timothy White, Kohler Co. business development manager for water technologies, displays disassembled PP components and the ceramic filter in the Kohler Clarity product being supplied at cost to help meet clean drinking water needs in Africa and Asia.
San Diego — Under a stewardship initiative, Kohler Co.’s Sheridan, Ark., plant has produced more than 5,000 ceramic water filtration systems since mid-March to help meet clean drinking water needs in Africa and Asia.
Kohler sells each 1-micron filtration system at a cost of about $ 17 to non-governmental relief organizations that buy, transport and distribute the systems, Timothy White, Kohler business development manager for water technologies, said in a June 7 interview at the Sustainable Brands event in San Diego.
Clear virgin food-grade polypropylene is used for water-touching parts and recycled PP for other components such as the colored lid and base.
White said work occurs at the Sheridan toilet-seat-making plant, Kohler’s center of excellence for plastics. Globally, privately held Kohler employs more than 32,000, operates in excess of 50 manufacturing facilities and is based in Kohler, Wis.
Kohler Clarity began as an idea of some employees visiting India and development work started in 2015.
Project contributors include health organization PATH of Seattle; Tufts University of Medford, Mass.; Industrial Molds Inc. of Rockford, Ill.; and non-profit World Vision Inc. of Federal Way, Wash.
Tufts’ department of civil and environmental engineering helped expand the testing capability of Kohler’s water quality laboratory in Wisconsin facilitating use of fluorescent microspheres to measure the reduction of various sized particles through the filter.
“Fluorescent spheres of different sizes — the same sizes as disease-causing organisms — are placed in influent water through the filter,” said Daniele Lantagne, an assistant professor at Tufts. “The water flows through the filter, and then the number of spheres remaining in treated water is estimated based on fluorescence.” This method measures the effect of filters in removing organisms via the size-exclusion filtration mechanism.
“Effective, simple-to-use durable filters are considered the best option for treating water at the household level to prevent the spread of infectious disease in areas without access to water and sanitation infrastructure,” Lantagne said via email, describing Kohler Clarity’s design as “a very promising filter that meets these criteria.”
In response to Kohler’s philanthropic request, Industrial Molds managed the tooling phase reviewing designs and handling feasibility issues. Industrial Molds obtained six molds — including two-cavity and four-cavity tools — from a joint-venture supplier in China.
Industrial Molds account managers Wes Stephens and Joe Hansen and two of Kohler’s Sheridan employees went to China to see injection mold trials and provide expertise when the mold maker experienced initial difficulties running the tools.
Industrial Molds donated the time of its management and tool makers and arranged for Kohler to acquire the molds at cost.
The project is a break-even for Kohler after factoring in the Industrial Molds’ donation, White said.
Each Kohler Clarity treatment tank holds up to 2.9 gallons of dirty water and has a ceramic filter cartridge. A gravity-fed safe storage container holds up to 3.1 gallons of clean water. A lip seal eliminates the entry of dust or pests.
The components are nest-able for shipping. “We try to fill a shipping container with 2,000 systems” to maximize efficiency, White said.
A system can make about 10.5 gallons daily. Kohler projects a well-maintained filter can process up to 1,321 gallons with service length on an average of one year.